Being attuned to how much your fabrication machinery costs to procure, run and maintain will help you to calculate costs, balance your budget and ultimately achieve a profit.
To that end, here are a few tricks to optimize your expenditure at every step and also keep tables on expenses so that you can detect when certain elements are becoming a burden on your budget.
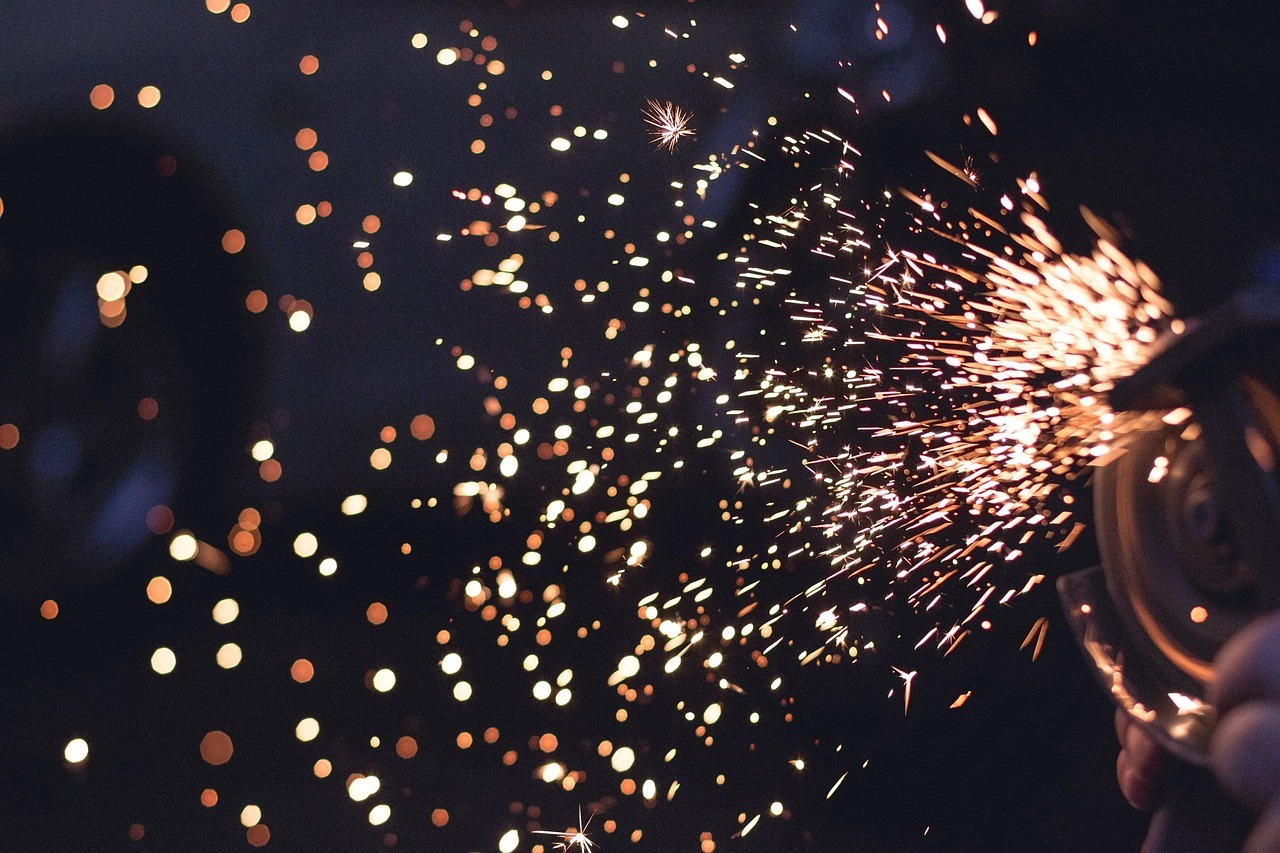
Buying and Selling Second Hand Machinery
Fabrication equipment costs can skyrocket if you only focus your attention on the new models that are available. Equally you may find that your output is suffering if you put up with older kit for longer because you feel that the cost of buying new is a prohibitive factor.
This is where buying used machines at Revelation Machinery and other online marketplaces makes a lot of sense. Whatever your fabrication requirements, you should be able to find the right equipment at a competitive price. Likewise you can also sell older units, recoup a bit of cash to then re-invest in your next purchase.
Paying attention to procurement costs and taking action to manage them through economically sound measures like buying and selling second hand will put you in a stronger position.
Schedule Maintenance to Avoid Disruption
Downtime is a significant cost to manufacturers, so planning for it to occur when machinery usage is at a minimum will reduce disruption and also keep expenses down.
There are clearly costs that go with maintaining and repairing existing fabrication equipment, which may make you hesitant to carry out necessary work on a consistent basis. However, the alternative is ignoring issues until it is too late, at which point your operations may grind to a halt if a machine fails in the middle of a shift and you are not prepared to deal with the fallout.
Creating a sensible maintenance schedule and sticking to it will help you to track costs more closely and ideally reduce them wherever possible by banishing machinery-related downtime altogether.
Monitor Material Consumption & Make Changes if Necessary
Another major expense associated with fabricating parts is that of the raw materials consumed in the production process.
In some cases it will not be possible to make changes to reduce the amount of material that is wasted, while in others you could curb your expenditure by migrating to a different approach.
For example, the rise of additive manufacturing in recent years has given businesses a fresh way to handle rapid prototyping and even fully-fledged production, all while minimizing the amount of waste that is generated. If this technology will fit your requirements, it could bring down material costs and help you to make each use of your fabrication equipment more profitable.
Wrapping Up
Ultimately the precise nature of the steps you take to track the cost of your fabrication equipment usage is not important; what matters most is that you are proactive in monitoring your expenses as well as in your efforts to fix any issues that are highlighted.