Warehouse operations and logistics firms benefit from implementing the latest tech innovations to gain a competitive edge in the market. Digital distribution and e-Commerce are booming, putting pressure on warehouse owners to achieve peak efficiency with their supply chain.
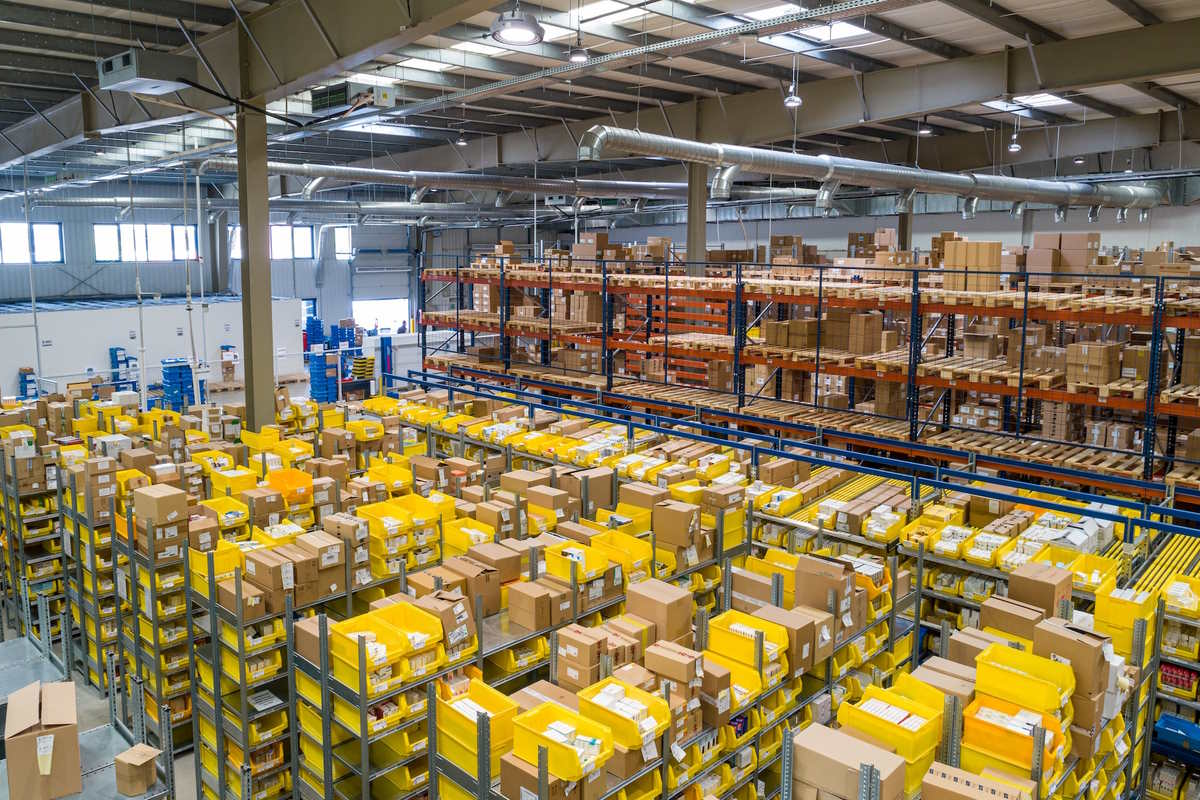
Organizational solutions such as bins, totes and dividers are the low-tech and economical start. They bring together safety, durability, cost-effectiveness and simplicity to warehousing. The upfront costs are low compared to high-tech solutions. In the long term, the benefits are more than obvious.
A bulk of warehouses reportedly plan to increase the spending on technology in the following years, so falling behind is not an option. Many self storage companies have also been improving their tech with cameras, keycodes and links to your phone.
1. Data interchange
Big data has spurred dynamic shifts across all industry sectors, and warehouses are no exception. EDI (Electronic Data Interchange) allows owners and managers to share documents between two computer systems. These files often involve purchase and shipping orders, stock transfer receipts, and shipping and inventory advice.
Integrating EDI into the warehouse management system (WMS) brings forth the seamless flow of information between different devices. This is made possible with solutions such as standard format and compatibility of EDI documents. Now all parties can collaborate more transparently and let the operations run like clockwork.
2. Enhanced Training Programs for Warehouse Staff
The digital revolution has not only transformed the hardware and software of warehouse operations but has also redefined the approach toward staff training and development. Among the innovative training methods being adopted, online certification programs stand out for their convenience and effectiveness. For instance, online scissor lift certification equips warehouse employees with the necessary skills and safety knowledge to operate scissor lifts efficiently. On the other hand, those who have completed online forklift certification programs have shown a higher level of accuracy and efficiency in their work.
This form of training ensures that warehouse personnel are up-to-date with the latest operational standards and safety regulations, thereby minimizing accidents and enhancing productivity. Adopting such digital training solutions represents a significant leap forward in preparing the workforce to meet the challenges of modern warehouse management.
3. Cloud Storage
Cloud storage solutions have induced similar developments and improvements in WMS. They make the data available at the fingertips to anyone with internet access and authorization. “Legacy systems” no longer cut it in the high-tech information age, and the switch to cloud technology is gaining momentum.
Self-updating and hosted computer systems bring down the cost of maintenance, labor, and infrastructure. Their cost-effectiveness comes from their ease of use, which means all staff members can contribute to the transition. Before making a decision, however, one needs to figure out who will own the data, have access to it, and where it will be physically stored.
4. Diligent drones
Drones have many possible applications, driving the accelerated automation process. These versatile airborne machines now handle demanding tasks that require many man-hours. For example, scanning the barcodes in the warehouse stacked to the roof is an ordeal for humans, who must utilize an elevated work platform or a forklift.
On the other hand, a drone carrying scanners can complete this activity in the same time it would take 80 workers to pull it off. Yet, before we witness widespread adoption, some challenges regarding safe navigation through the warehouse remain to be tackled.
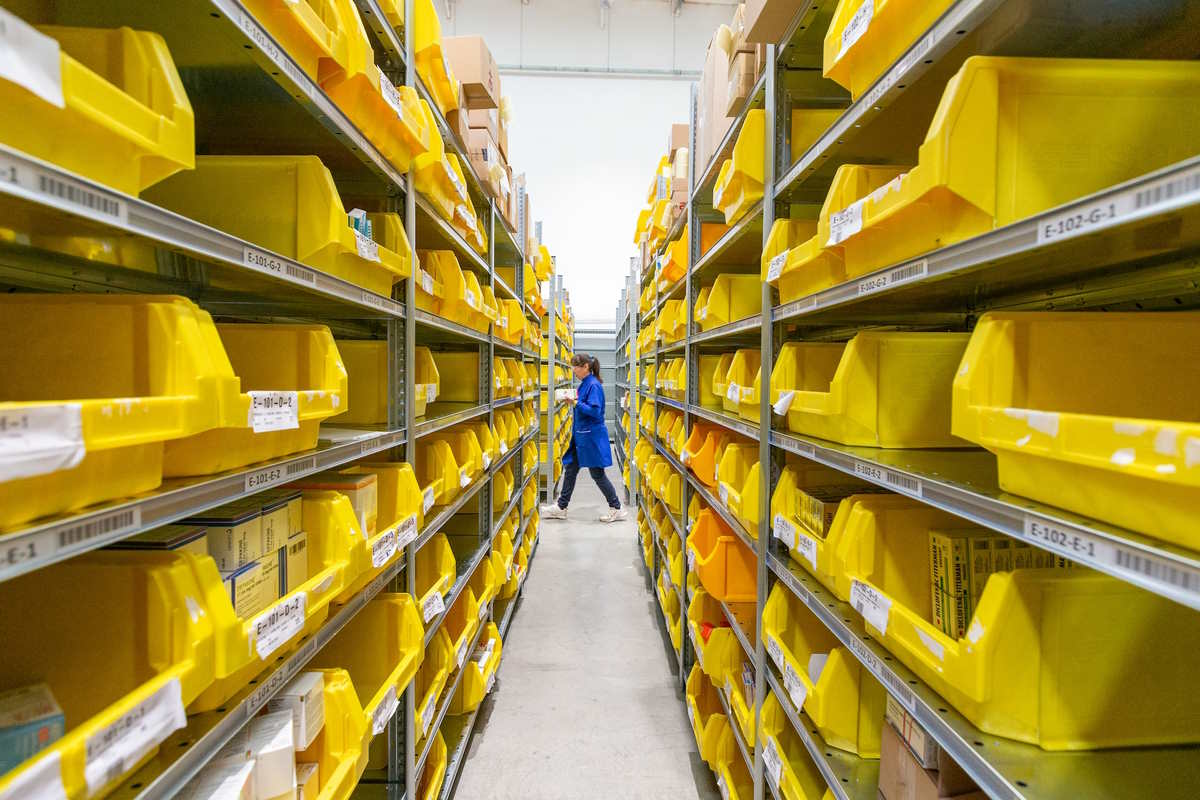
5. The Age of the Robots
To reap the benefits of full automation, warehouses are investing in robotics. Manufacturers from Kiva Systems provide robots capable of managing inventory, picking and stock take. Amazon’s small orange machines have a defined area of operations, learn where to take inventory from, and take it to the workers.
They have a pallet-like object on the back and move around the facilities with ease. This transformation from the man-to-goods process to goods-to-man marks the dawn of the revolution in logistics. There are many other examples of autonomous mobile robotics (AMR), letting business owners accomplish high volumes of small, multi-line orders and satisfy the rising demand.
6. High-tech lift trucks
The lift truck market is undergoing rapid growth, with new cutting-edge products flooding the market. First attempts to use tablets on these vehicles were not overly successful, but today’s specialized device mounts can withstand shocks and vibrations. Thus, full time-use of portable devices has become a reality, speeding up data collection.
Armored tablets are put on forklifts and other workhorse vehicles, enhancing the efficiency across the warehouse. Furthermore, many lift trucks now have digital controls that are easier to read and calibrate. Finally, experts argue that hydrogen cell forklifts will outpace gas-powered models. These killer machines are already used in large-scale operations of BMW, Walmart and Coca-Cola.
May the Tech Force be With You
Technology is a major force in warehouses and logistics and is used to make operations future-proof. One must not miss the chance to boost the level of performance and flexibility, as well as data sharing. Each component of the supply chain must work like a charm, and human workers are now accompanied by drones and robot helpers, creating a whole new warehouse landscape. The upcoming advances and novelties will continue to influence operations across the globe, so do not let budgetary constraints pose a hurdle on the road to success.