Industrial manufacturing relies heavily on innovation. Manufacturers are always on the lookout for ways to improve products, reduce production times, and cut costs. Rapid prototyping has emerged as an innovative technique that’s revolutionizing product design, testing, and eventually manufacturing processes.
In this blog post, we’ll delve deeper into this captivating field and examine its immense impact on industrial manufacturing.
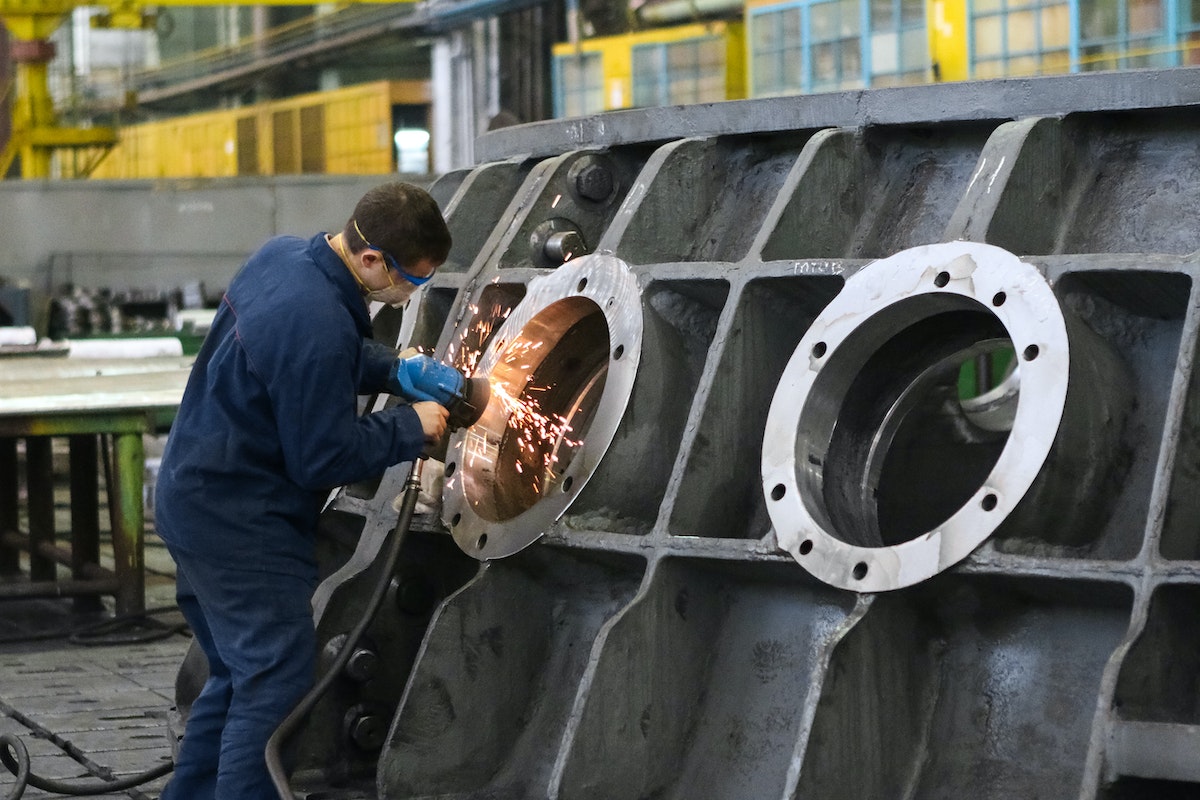
The Evolution of Rapid Prototyping
Rapid prototyping has grown increasingly popular. The global rapid prototyping market was valued at $2.5 billion in 2021 and is projected to grow to $15 billion by 2031.
Rapid prototyping involves the rapid fabrication of physical parts, models, or assemblies using computer-aided design (CAD). The creation of the part, model, or assembly is usually completed using additive manufacturing or 3D printing.
This efficient process significantly shortens the time from conception to market for products, giving companies an advantage in competitive markets. For in-depth knowledge of rapid prototyping, make sure to visit website pages from various rapid prototyping companies and explore their wealth of information. These professionals offer comprehensive resources and expertise that can provide invaluable insights into how this approach to manufacturing can revolutionize your efforts.
What Is Industrial Manufacturing?
To understand how rapid prototyping relates to industrial manufacturing, you must first understand large-scale production. This service entails turning raw materials into finished products used by various machines and tools. Experts specialize in this service for manufacturing products for important economic sectors like automotive and aerospace manufacturing, consumer electronics production, food, pharmaceuticals, and consumer electronics, as well as more general uses like construction.
Industrial manufacturing involves several steps, from component evaluation and assessment to final assembly. The product design and engineering process also involves troubleshooting technical specs, structuring processes, scheduling runs, and overseeing testing. Rapid prototyping is crucial in this case.
Quality control is the next step after machining and fabrication. It can consume a large portion of any budget. This option allows companies to move quickly from the early stages of development to distribution, without wasting resources or time on unnecessarily long processes.
Teams can use advanced fabrication techniques and industrial manufacturing technologies to develop, evaluate, or improve complex concepts. To control outcomes and optimize detail, they often combine CAD, computer-assisted manufacturing (CAM), digital image systems, 3D printing, and robots.
Importance of Rapid Prototyping in Industrial Manufacturing
Industrial manufacturing strives to achieve high production efficiency, cost-effectiveness, and consistency with timely deliveries to on-demand markets. This is not feasible with most traditional manufacturing methods. Rapid prototyping has quickly become the standard in product design, mass production, and for companies competing in competitive industries.
- Faster design iterations: Create physical prototypes quickly to test, collect feedback, and modify.
- Shorten development time: This allows for faster time to market-ready inventory.
- Reduce manufacturing costs: Identify early concerns to minimize errors and rectify issues before costly investments.
- Accurate validation of design: Rapid prototyping allows for a physical representation of the product to be evaluated and approved.
- Efficient product optimization: Determine the best solutions by experimenting and refining.
Rapid Prototyping Techniques in Industrial Manufacturing
In industrial manufacturing, rapid prototyping encompasses a variety of processes that allow for the creation of digital models and physical prototypes quickly and efficiently. The use of advanced techniques is crucial to accelerating product design, improving validation, and increasing productivity. Here are some of the most common RP techniques used in industrial manufacturing:
- 3D Printing
- Computer Numerical Control
- Selective laser sintering
- Stereolithography (SLA)
Rapid prototyping for industrial manufacturing helps accelerate product development cycles and fosters seamless collaboration through the cross-pollination of ideas. RP creates a collaborative environment that allows better questions and answers to emerge.
Applications in Industrial Manufacturing
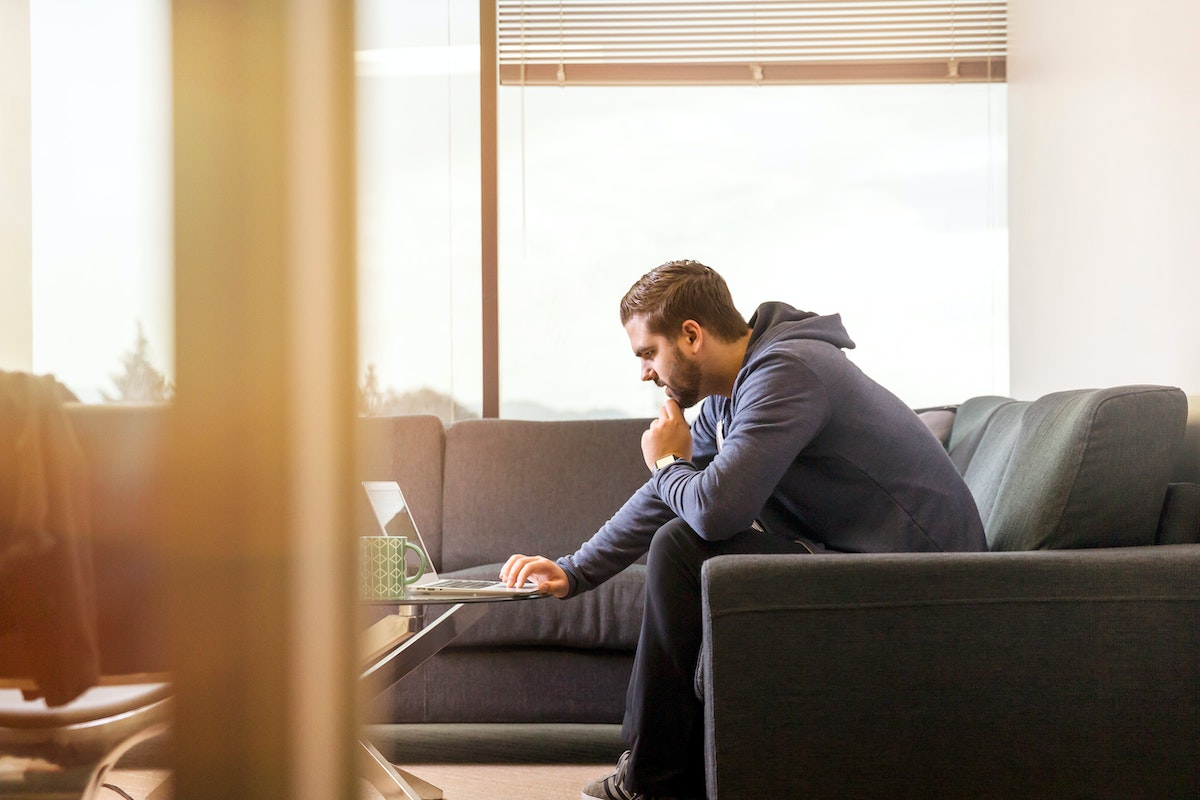
Rapid prototyping has found applications in various industries, fundamentally changing the landscape of industrial manufacturing. In the aerospace industry, where precision and lightweight components are paramount, rapid prototyping allows engineers to create complex parts with reduced weight and improved performance. It also facilitates the testing of aerodynamic designs and engine components.
Automotive manufacturers often utilize rapid prototyping to develop and test prototypes of car parts such as interior components, engine parts, and entire vehicle prototypes quickly, speeding up their design processes and helping bring new models faster to market.
Rapid prototyping has also transformed healthcare production of custom medical devices like prosthetics, dental implants, and orthopedic implants. Furthermore, rapid prototyping serves a significant purpose by creating anatomical models for surgical planning and medical education purposes.
Rapid prototyping has become an invaluable asset in the development of consumer electronics, allowing manufacturers to quickly produce prototypes of smartphones, tablets, wearables, and other electronic devices. This expedites the product development cycle in a highly competitive industry.
Final Thoughts
Rapid prototyping has revolutionized industrial manufacturing by offering speed, flexibility, and cost efficiency. It has opened the way to innovation across industries while empowering designers and engineers to produce products once considered unfeasible.
As technology evolves and material science grows, rapid prototyping will play an increasingly vital role in shaping the future of manufacturing. Therefore, manufacturers that want to stay relevant must embrace this transformative technology as soon as possible.