In the realm of manufacturing, high-precision metrology plays a key role in upholding stringent quality standards for products. Technological advancements have paved the way for manufacturers to achieve heightened levels of accuracy and precision, ultimately leading to enhanced product performance and increased customer satisfaction. In this article, we will delve into the importance of high-precision metrology in advancing the quality of manufacturing processes.
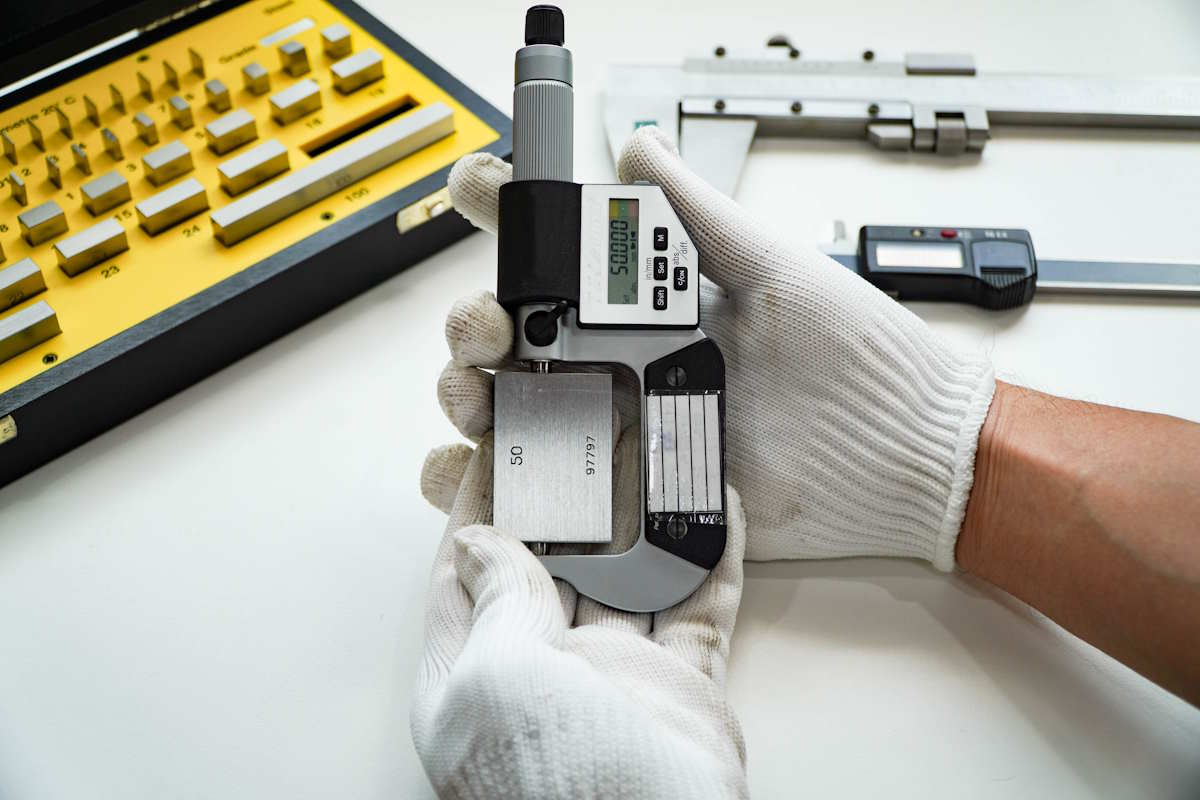
The Significance of Precision
Precision stands as a cornerstone in manufacturing as it ensures that products are crafted with attention to detail. Through high-precision metrology, manufacturers gain the ability to measure and regulate every facet of their production procedures accurately. Whether it involves taking measurements of components or tuning machinery settings, accuracy remains paramount. Manufacturers can verify that their parts align with tolerances by utilizing measurement tools like coordinate measuring machines (CMMs) and laser scanners. This proactive approach helps prevent products from reaching consumers, diminishing the likelihood of product recalls, warranty issues, and harm to brand reputation.
Enhancing Product Performance
High-precision metrology solutions empower manufacturers to evaluate whether their products meet predefined performance benchmarks. Rigorous measurement methods facilitate an examination of attributes such as dimensions, surface texture, straightness, flatness, parallelism, and perpendicularity. By ensuring adherence to specifications outlined by design engineers and industry standards, manufacturers elevate the quality of their products.
Furthermore, advanced inspection tools play a crucial role in identifying deviations or defects that could affect a product’s performance. By catching these issues, manufacturers can rectify them before the final product reaches customers.
Maintaining Quality Control Throughout Production
The use of high-precision measurement techniques goes beyond conducting checks on completed products; it also involves monitoring various stages during manufacturing, such as inspecting incoming materials. If materials or parts sourced from suppliers lack quality control measures, it can introduce inconsistencies in the production process, resulting in subpar end products.
In the end stages of production, such as assembly or machining, leveraging precise calibration equipment empowers producers to proactively address issues related to process stability, accuracy, and enhancement. Aligning components based on measurements ensures that assemblies fit precisely and function correctly. Similarly, calibrating machining tools helps uphold uniformity and reduce variations in manufactured parts, significantly boosting quality.
Enhancing Efficiency and Cost Efficiency
High-precision measurement techniques also target process optimization by minimizing waste and inefficiencies. The precise data gathered during inspections allows manufacturers to make informed decisions about adjusting processes or implementing improvements that boost productivity and quality simultaneously.
For instance, conducting the analysis can aid in pinpointing the root causes of variability along a production line, thereby improving maintenance schedules for equipment and streamlining troubleshooting methods to accelerate defect detection efforts. This proactive approach minimizes waste like scrap materials or rejected parts due to precision controls and saves manufacturers time, resources, and expenses linked to rework or replacements.
Furthermore, the use of high-precision metrology supports the application of statistical process control techniques. By monitoring dimensions and performance parameters, manufacturers can swiftly identify deviations from acceptable quality standards. Leveraging this real-time data to make immediate adjustments in manufacturing processes boosts both quality assurance through defect prevention and operational efficiency by minimizing disruptions.
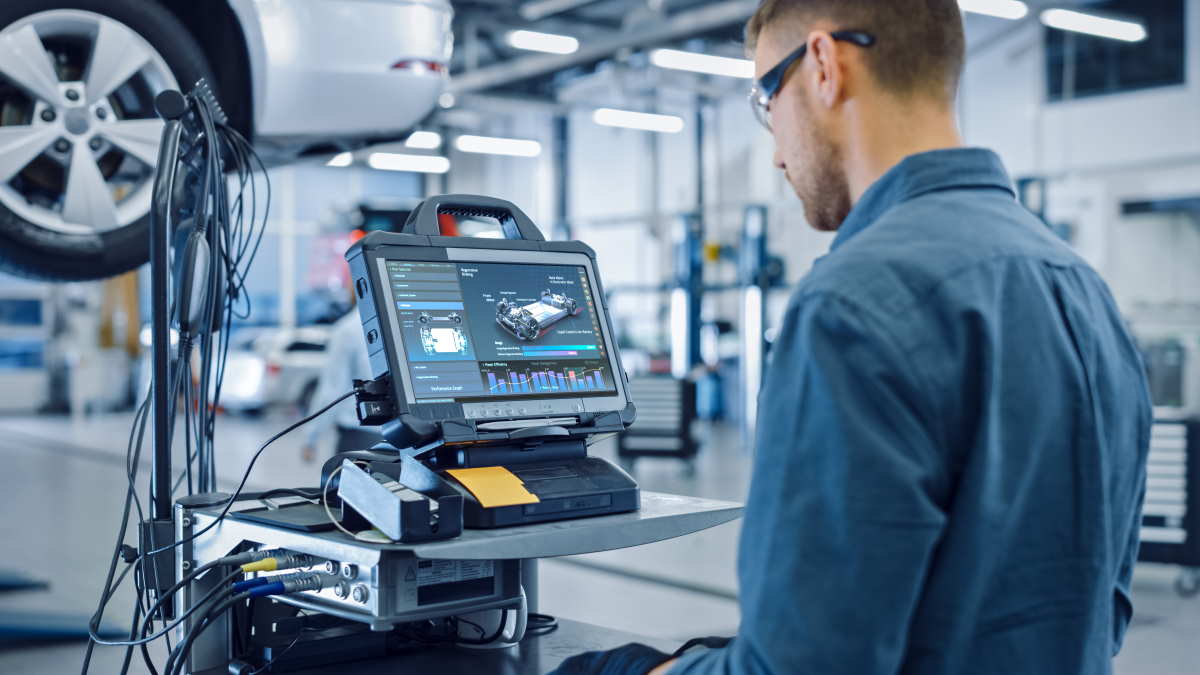
Employing High Precision Metrology in Product Design and Innovation
High-precision metrology plays a critical role not only in the final stages of production but also in product design and innovation processes. Integrating measurement methods during the design phase enables manufacturers to ensure that their products are both feasible for production and capable of meeting performance criteria.
During prototyping phases, sophisticated metrology tools empower designers to validate their concepts by measuring features and evaluating performance metrics. This approach aids in identifying any design shortcomings or areas that could be enhanced before transitioning into mass manufacturing. Engaging in intervention can help save time and money that would otherwise be used to adjust tools or redesign components later in the manufacturing process.
Conclusion
High-precison metrology plays a key role in the manufacturing sector by ensuring that products are crafted within the tolerance limits specified by design engineers. This precision brings about advantages such as improved product performance, heightened customer satisfaction, enhanced efficiency, and cost-effectiveness.
By investing in inspection tools and calibration equipment at every stage of production—from checking materials to assembling the final product—manufacturers can uphold strong quality control practices across their operations. Consequently, they can consistently deliver top-notch products that meet customer demands while minimizing waste resulting from defects or inefficiencies.