The integration of robotics into industrial processes has revolutionized the way we manufacture and produce goods. Robotics technology has come a long way from its early days, now playing a crucial role in various industries worldwide. This technological advancement has become essential for companies aiming to stay competitive and efficient in a fast-paced market. The use of robots in industrial processes offers numerous benefits, enhancing productivity, quality, safety, and cost-effectiveness. Here are some key benefits of integrating robotics into industrial processes and how they contribute to a more efficient and reliable manufacturing environment.
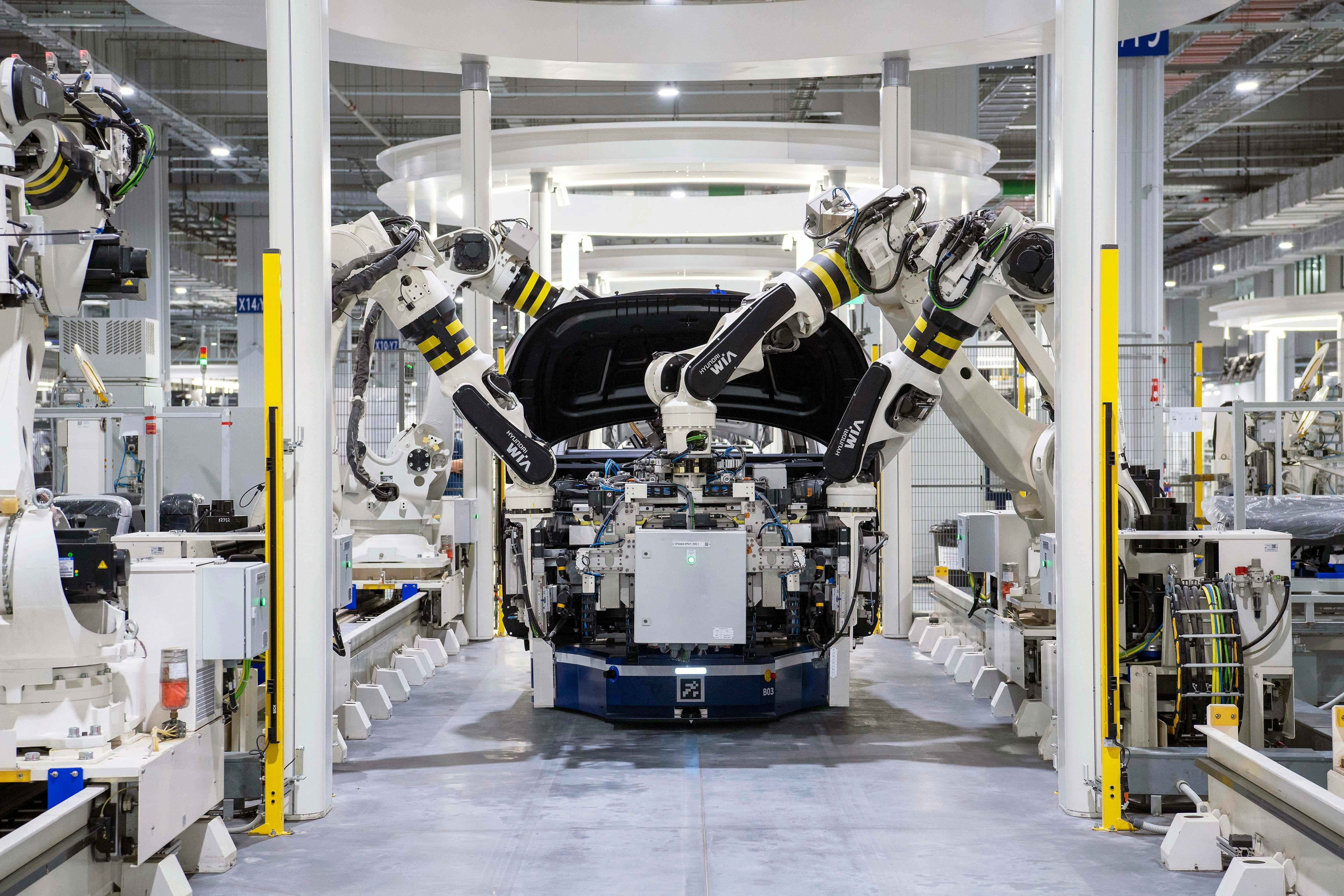
1. Increased Efficiency & Productivity
One of the primary advantages of using robotics in industrial processes is the significant boost in efficiency and productivity. Robots are capable of working around the clock without the need for breaks or rest, unlike human workers. This continuous operation ensures that production lines can run smoothly and consistently, meeting high demands and tight deadlines.
These tasks require precision and speed, which robots can provide without fatigue or error. As a result, companies can produce more units in less time, increasing overall output and meeting customer demands more effectively.
2. Quality & Consistency
Another major benefit of industrial automation through robotics is the improvement in product quality and consistency. For instance, servo motors play a crucial role in industrial automation by providing precise control of movement and shaft positioning in various applications.
Robots are programmed to perform tasks with high precision, reducing the risk of human error that can lead to defects and inconsistencies. This level of accuracy ensures that each product meets the same high standards, enhancing the overall quality of the final output.
The precision of robots ensures that each component is placed correctly, resulting in reliable and high-quality products. Consistent quality also helps in building customer trust and brand reputation, which is crucial for business success.
3. Enhanced Safety for Workers
Safety is a top priority in any industrial setting, and robotics technology plays a significant role in enhancing workplace safety. Robots can take over dangerous and hazardous tasks that pose risks to human workers. By performing these tasks, robots help to minimize the occurrence of workplace accidents and injuries.
In industries such as chemical manufacturing or metalworking, robots are used to handle toxic substances or operate heavy machinery. These tasks can be extremely dangerous for human workers, but robots can perform them with ease and without risk. This not only protects workers from potential harm but also contributes to a safer working environment overall.
4. Cost Savings in the Long Run
While the initial investment in robotics technology can be substantial, the long-term cost savings are significant. Robots can help companies save money in various ways, such as:
- Reducing Labor Costs
- Minimizing Downtime
- Increasing Efficiency, etc.
Over time, these savings can outweigh the initial investment, making robotics a cost-effective solution for many industries. These tasks are repetitive and time-consuming, but robots can perform them quickly and accurately. By automating these processes, companies can reduce the need for manual labor, lowering labor costs and increasing overall productivity.
5. Flexibility & Scalability
Robotics technology offers a high degree of flexibility and scalability, allowing companies to adapt to changing demands and production requirements. Robots can be programmed to perform various tasks, making it easy to switch between different production lines or processes. This adaptability is essential for industries that need to respond quickly to market changes or customer needs.
For example, in the pharmaceutical industry, robots are used for tasks such as filling and packaging medications. The flexibility of robots allows companies to adjust production volumes based on demand, ensuring that they can meet customer needs efficiently. Additionally, as companies grow, robots can be scaled up to handle increased production without significant changes to the existing setup.
6. Data Collection & Analysis
One of the key benefits of integrating robotics into industrial processes is the ability to collect and analyze data more effectively. Robots equipped with sensors and monitoring systems can gather real-time data during production. This data can be used to monitor performance, identify inefficiencies, and make informed decisions to improve processes.
For example, in the automotive industry, robots collect data on assembly line performance, such as speed, precision, and error rates. This information can be analyzed to optimize operations, reduce downtime, and enhance overall efficiency. Better data collection and analysis help companies maintain high standards and continuously improve their production processes.
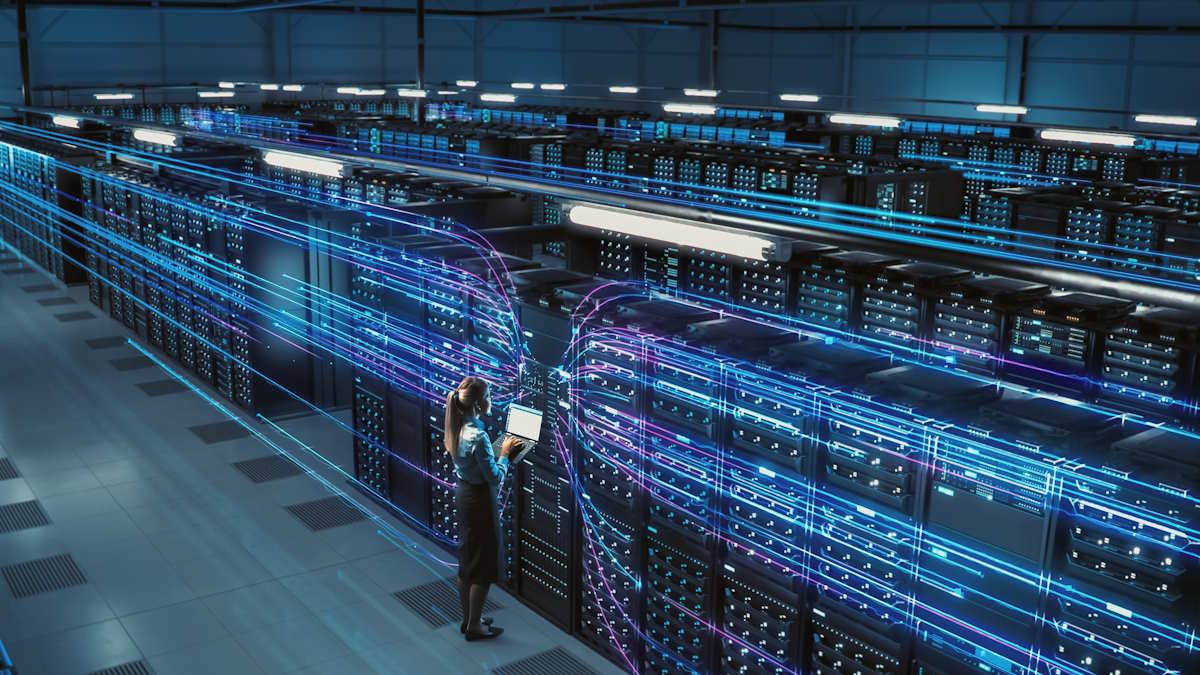
7. Competitive Advantage
Integrating robotics into industrial processes can give companies a significant competitive advantage. By adopting advanced technologies, businesses can stay ahead of competitors and meet customer demands more effectively. Robotics can help companies offer higher-quality products, faster delivery times, and more reliable services.
For instance, in the consumer electronics industry, companies using robotics can produce devices with greater precision and consistency. This leads to better product quality and customer satisfaction. By staying at the forefront of technology, these companies can attract more customers and maintain a strong market position.
8. Environmental Benefits
Robotic technology can also contribute to environmental sustainability. Robots can perform tasks with high precision, reducing waste and minimizing the use of resources. Additionally, robots can operate more efficiently, consuming less energy compared to traditional manufacturing methods.
By integrating robotics into their processes, companies can work towards more sustainable practices, which is increasingly important in today’s environmentally conscious market.
9. Future-Proofing Industrial Processes
As industries evolve and new technologies emerge, it is essential for companies to future-proof their processes. Integrating robotics is a crucial step in preparing for the future of manufacturing. Robots can be easily updated with new software and capabilities, ensuring that they remain relevant and effective.
This flexibility allows them to stay competitive and meet the demands of a constantly changing market. Future-proofing with robotics ensures that companies are ready for the next wave of industrial innovation.
10. Collaboration with Robots
Modern industrial processes benefit greatly from enhanced collaboration between humans and robots. This collaboration allows for the combination of human creativity and problem-solving skills with the precision and efficiency of robots. By working together, humans and robots can achieve better results than they could alone.
Surgeons can control robotic systems to make precise movements, leading to improved patient outcomes. This synergy between human expertise and robotic precision exemplifies the potential of collaborative industrial processes.
Let’s Wrap Up
Integrating robotics into industrial processes offers numerous benefits that can transform the way companies operate.
As technology continues to advance, the role of robotics in industry will only become more prominent. Businesses that embrace robotics can stay competitive, meet customer demands more effectively, and prepare for future challenges.