In a bustling factory, the hum of machines is no longer dominated by the clatter of traditional manufacturing equipment but by the precise and almost silent movements of industrial robot arms. These robotic systems, once a futuristic concept, are now an integral part of the modern manufacturing landscape, revolutionizing the way products are made. As companies seek to remain competitive in a global market, the adoption of these advanced technologies is becoming not just an option but a necessity.
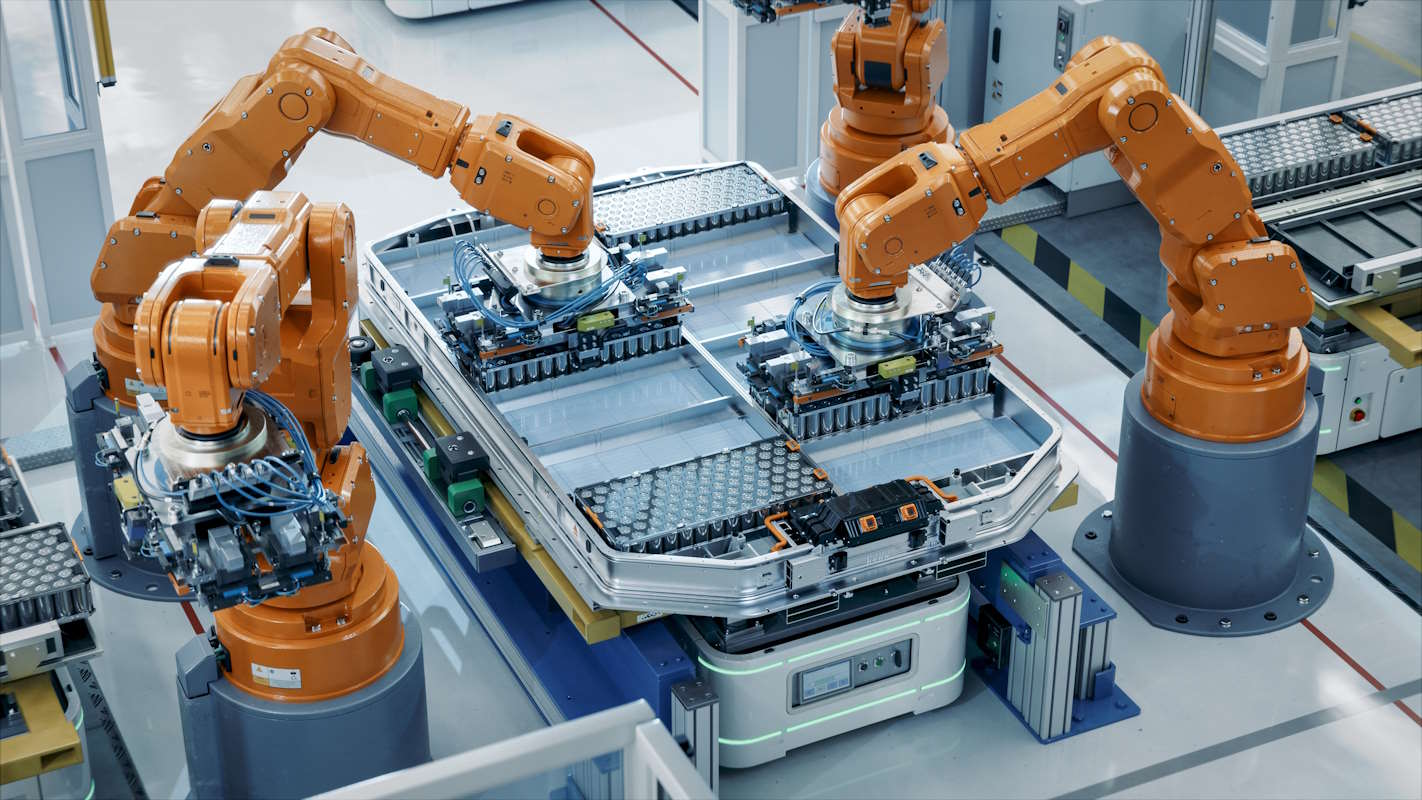
The rise of industrial robot arms has brought about a profound transformation in manufacturing. From increasing productivity and efficiency to ensuring greater precision and consistency, these robots are changing the face of production floors worldwide.
As we delve deeper into this transformation, it’s clear that the integration of automation robotics into manufacturing processes is reshaping industries, workforce dynamics, and even the global economy.This article explores the evolution of industrial robot arms, their impact on manufacturing efficiency, the flexibility they offer in production, the implications for the workforce, and the challenges that accompany their adoption.
The Evolution of Industrial Robot Arms
Industrial robot arms have advanced dramatically since their introduction in the 1960s. The first industrial robot, Unimate, marked the dawn of a new era in manufacturing by automating dangerous or repetitive tasks. Over the years, advancements in computing, sensors, and artificial intelligence (AI) have made these robots more versatile and efficient.
Today, modern robot arms are equipped with sophisticated sensors and AI algorithms, enabling them to perform tasks with extraordinary precision and adapt to new environments. The rise of collaborative robots, or cobots, further illustrates this evolution. Designed to work safely alongside human workers, cobots are transforming production processes by allowing greater flexibility and human-robot collaboration.
The Impact on Manufacturing Efficiency
One of the most notable benefits of industrial robot arms is the significant increase in productivity they bring to manufacturing. By automating repetitive tasks, robots reduce production times and increase output, especially in industries where speed and precision are critical, like electronics and automotive manufacturing.
In addition to boosting productivity, robots enhance precision, which is crucial in industries like semiconductor manufacturing, where even minor errors can be costly. Robots perform tasks with micron-level accuracy, ensuring products meet stringent quality standards and reducing material waste.
While the initial investment in robot arms can be high, the long-term cost savings are considerable. Reduced labor costs, improved efficiency, and minimized waste lead to substantial returns on investment, making these technologies increasingly attractive to manufacturers.
Flexibility and Customization in Production
The flexibility offered by industrial robot arms is another key factor driving their adoption. Unlike traditional machinery, which is often designed for specific tasks, modern robot arms can be reprogrammed and reconfigured for various applications. This adaptability is crucial in industries that require frequent changes in production processes, such as consumer electronics.
In today’s fast-paced market, the ability to quickly adapt to changing demands is vital. Industrial robots can switch between tasks or products in real-time, enabling manufacturers to respond to market trends and customer needs effectively. This capability is particularly valuable for producing small batches of customized products without sacrificing efficiency.
Scalability is another advantage, as robots can be easily integrated into production lines to meet increasing demands. The integration of industrial robots with the Internet of Things (IoT) and smart manufacturing systems further enhances production processes by enabling real-time monitoring and adjustments.
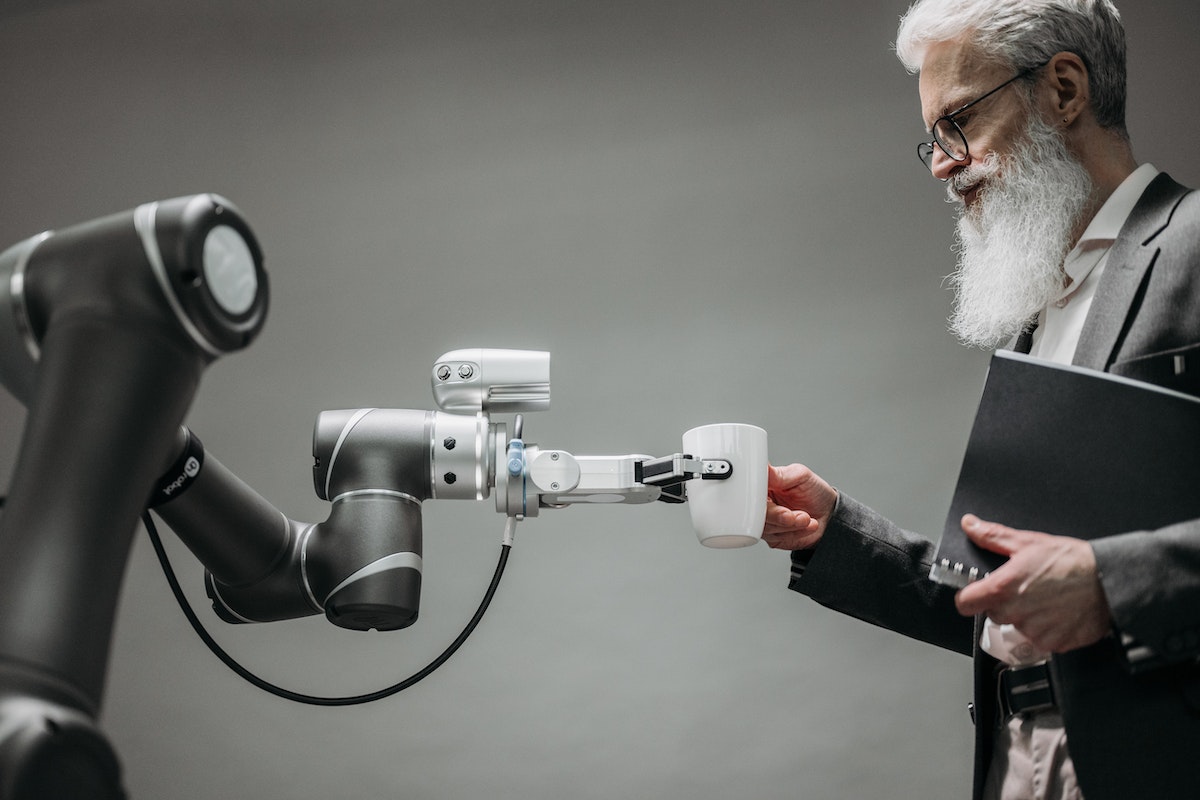
Workforce Implications
The rise of industrial robot arms has significant implications for the workforce. As robots take over repetitive tasks, the roles of human workers are shifting towards technical and supervisory positions. This transition requires upskilling and reskilling to prepare workers for an increasingly automated environment.
Collaborative robots have also changed workplace dynamics by enabling safer and more efficient human-robot collaboration. However, this shift raises important safety considerations, and companies must ensure proper measures are in place to protect both human workers and robots.
Despite the benefits of automation, there are concerns about job displacement and economic inequality. As robots become more prevalent, some workers, particularly in low-skill positions, may find their jobs at risk. Addressing these challenges requires investment in education and training programs to prepare workers for the future.
Challenges and Considerations
While industrial robot arms offer numerous benefits, their adoption comes with challenges. High initial costs can be a significant barrier for small to medium-sized enterprises (SMEs), making it difficult for them to compete with larger companies. However, government incentives and financing options are available to help SMEs overcome these hurdles.
Integrating robots into existing manufacturing systems can also be complex and time-consuming. Companies must plan carefully to ensure seamless integration with other equipment and systems, often requiring custom engineering solutions and ongoing maintenance.
Ethical and social considerations, such as job displacement and economic inequality, are also critical as automation becomes more widespread. Policymakers, business leaders, and society must work together to develop strategies that balance the benefits of automation with the need to protect workers and ensure a fair distribution of its advantages.
The Future of Manufacturing with Industrial Robots
As industrial robot arms continue to evolve, the future of manufacturing is set to become even more automated and efficient. The development of fully automated “lights-out” factories, where production continues without human intervention, is pushing the boundaries of what is possible in manufacturing. These factories represent the next step in automation, where AI-driven robots and smart systems work together to create highly efficient production environments.
Globally, the impact of industrial robot arms is significant. Automation is leveling the playing field between developed and developing countries, allowing manufacturers in less industrialized regions to compete globally. Additionally, as labor costs rise in traditionally low-cost manufacturing hubs, robots are facilitating the reshoring of jobs to countries with higher labor costs but advanced automation capabilities.
Conclusion
Industrial robot arms are transforming manufacturing by increasing efficiency, precision, and flexibility. While their adoption presents challenges, careful management can ensure that the benefits of automation robotics are shared broadly across society. As technology advances, the role of industrial robots in manufacturing will continue to grow, shaping the future of production worldwide.