Ensuring product quality and precision in industries heavily relies on inspection importance. This process involves checking if the components meet the criteria to guarantee fit and function. Various tools are utilized to obtain measurements during inspections. This piece delves into the tools commonly employed for inspections and their operational mechanisms and discusses the technology that drives them.
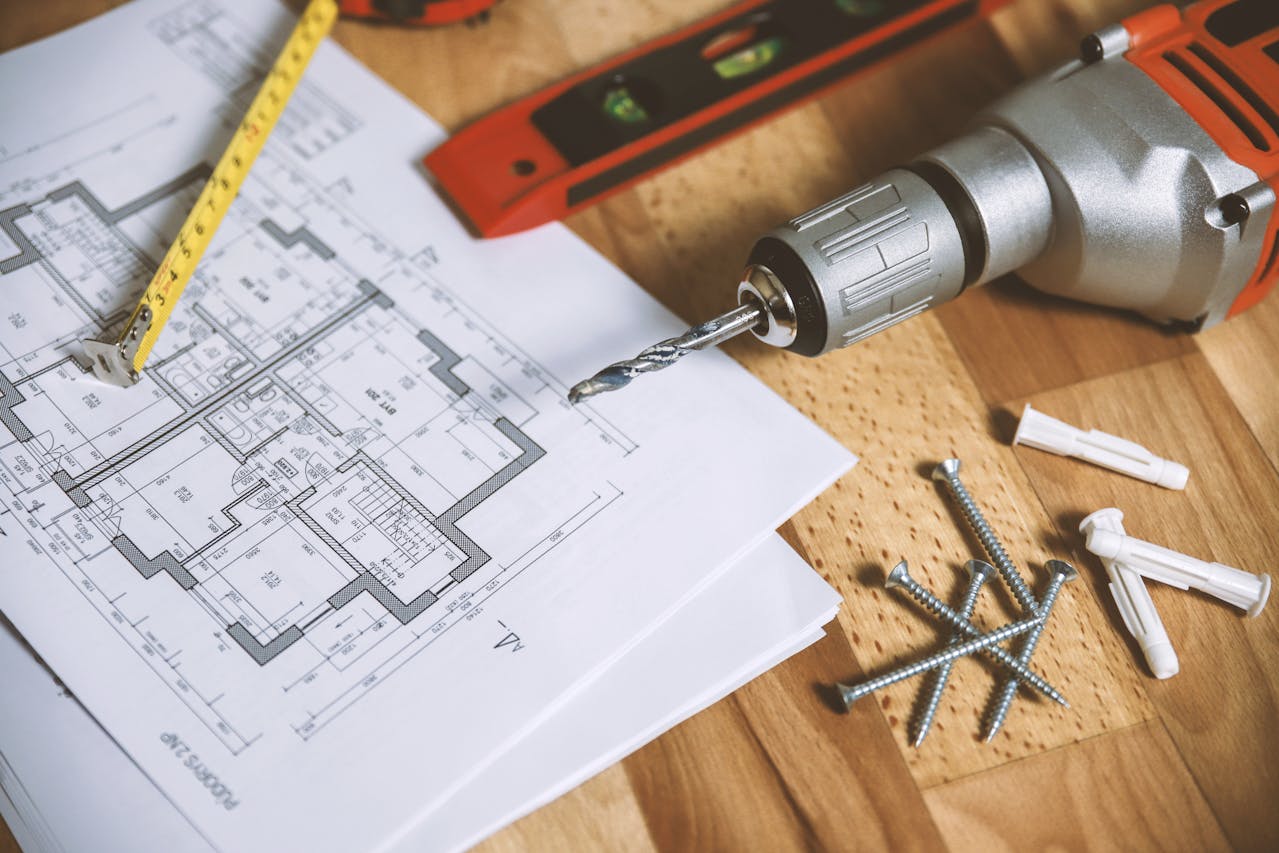
Calipers
Calipers are known for their versatility in inspections and are considered essential tools in the field. They come in digital, dial, and vernier variations. Calipers measure the distance between two opposite sides of an object. Users can adjust the movable jaw to measure external dimensions and depths. Digital calipers provide readings that minimize errors and improve accuracy. On the other hand, analog dials and vernier calipers require skillful operation but can still deliver dependable measurements when used properly in dimensional inspection.
Micrometers
Using micrometers enhances the precision of inspections by providing a level of accuracy in measurements. These instruments are particularly effective at gauging distances with precision, often achieving readings as precise as one-thousandth of a millimeter. The spindle and anvil are adjustable to secure the object being measured. The measurement is shown on either a scale or a digital display. While external micrometers are used for measuring dimensions, internal micrometers are designed for measuring precise dimensions.
Height Gauges
Height-measuring tools measure the height of objects and are commonly utilized on a flat surface for this purpose. These tools typically include a marking tool that accurately marks points on the object being measured. Users can determine the height measurement by observing the movement of the marking tool on the tool along with readings displayed on either a scale or digital screen.
Coordinate Measuring Machines (CMMs)
Coordinate Measuring Machines (CMMs) have transformed the way dimensional inspections are conducted by providing precise and accurate measurements. These machines employ a probing system to assess the characteristics of objects by gathering data points on surfaces. CMMs translate data into details through software integration capabilities for analyses and comparisons with design standards. Their ability to reduce mistakes and enhance productivity has made CMMs essential in sectors that demand measurements.
Laser Scanners
Noncontact measurement capabilities have led to the increasing use of laser scanners in industries like automotive and aerospace for quality control purposes. Laser scanners work by projecting a laser beam onto the surface of an object and capturing data points from the reflected light to create a 3D model that accurately depicts the object’s dimensions and intricate shapes.
Optical Comparators
Optical comparators, known as profile projectors, present a method for conducting inspections by projecting an enlarged outline of an object onto a screen for comparison with a standard template image to effectively detect any deviations in shape or size. This tool is especially valuable for examining parts and validating profiles.
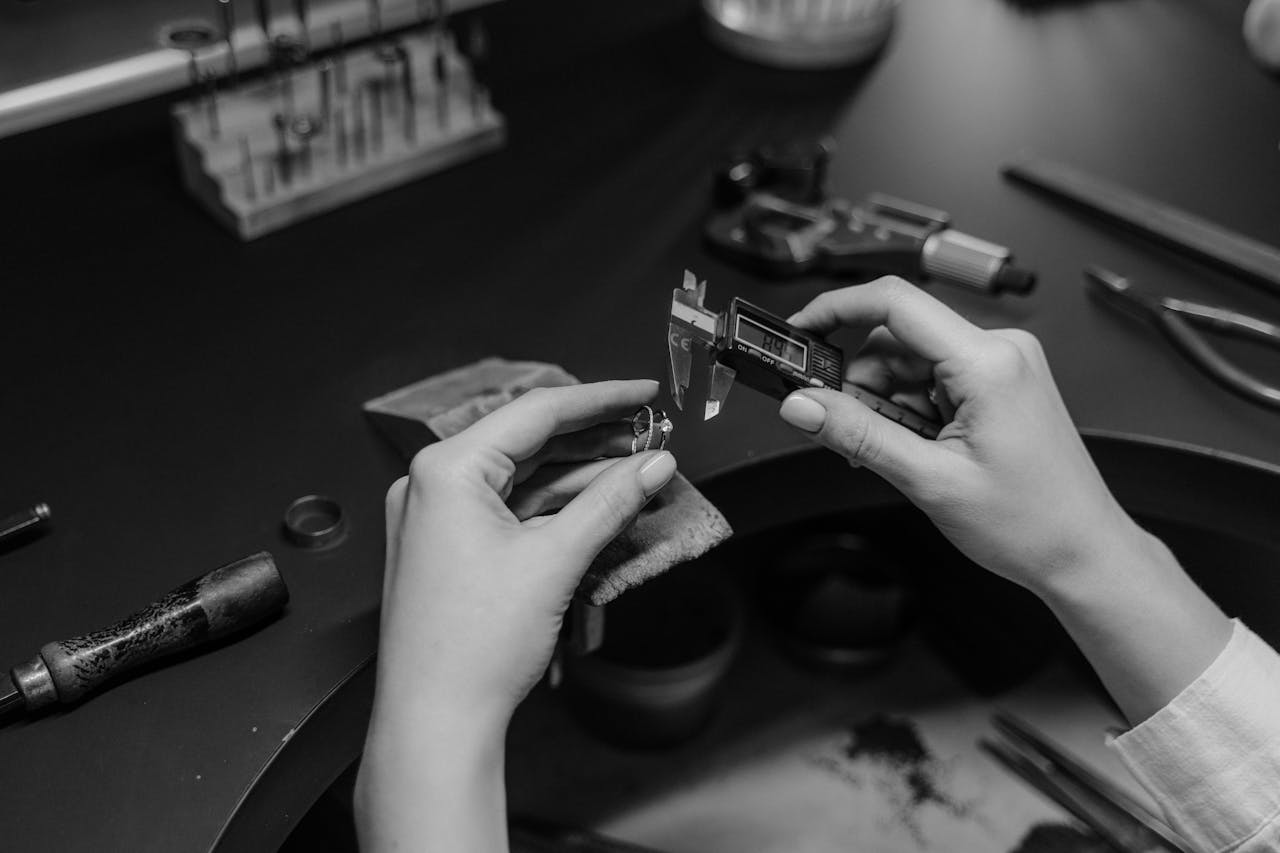
Surface Plates
Surface plates are not just instruments for measuring; they are tools in the inspection process that provide a reference point for measurements using materials like granite or cast iron. Inspectors rely on these steady surfaces to verify the precision of tools like height gauges and dial indicators. The level and steadiness of surface plates are essential for upholding the reliability of measurements.
Dial Indicators
Dial gauges provide readings of distances or shifts in an object’s placement by utilizing a dial display and a plunger to track dimensional changes while moving across the surface of the object. These instruments are commonly used to measure deflection or alignment in machinery to guarantee that parts meet required tolerances. Their versatility and precision make them essential tools in manufacturing and maintenance environments.
Conclusion
Tools utilized in checks offer a level of accuracy and precision that ensures quality control in various sectors of industry diversity. Each tool presents features that cater to measurement requirements, ranging from calipers and micrometers to cutting-edge technologies such as CMMs and laser scanners. Grasping the purpose and practicality of these tools empowers professionals to conduct inspections and guarantees that products adhere to criteria.