Precision and customization are critical for success. Whether it’s in healthcare, electronics, automotive, or consumer goods, small-part molding plays a vital role in creating components with exact specifications and unmatched quality. Custom small-part molding solutions cater to a variety of industries, offering innovative approaches to manufacturing challenges.
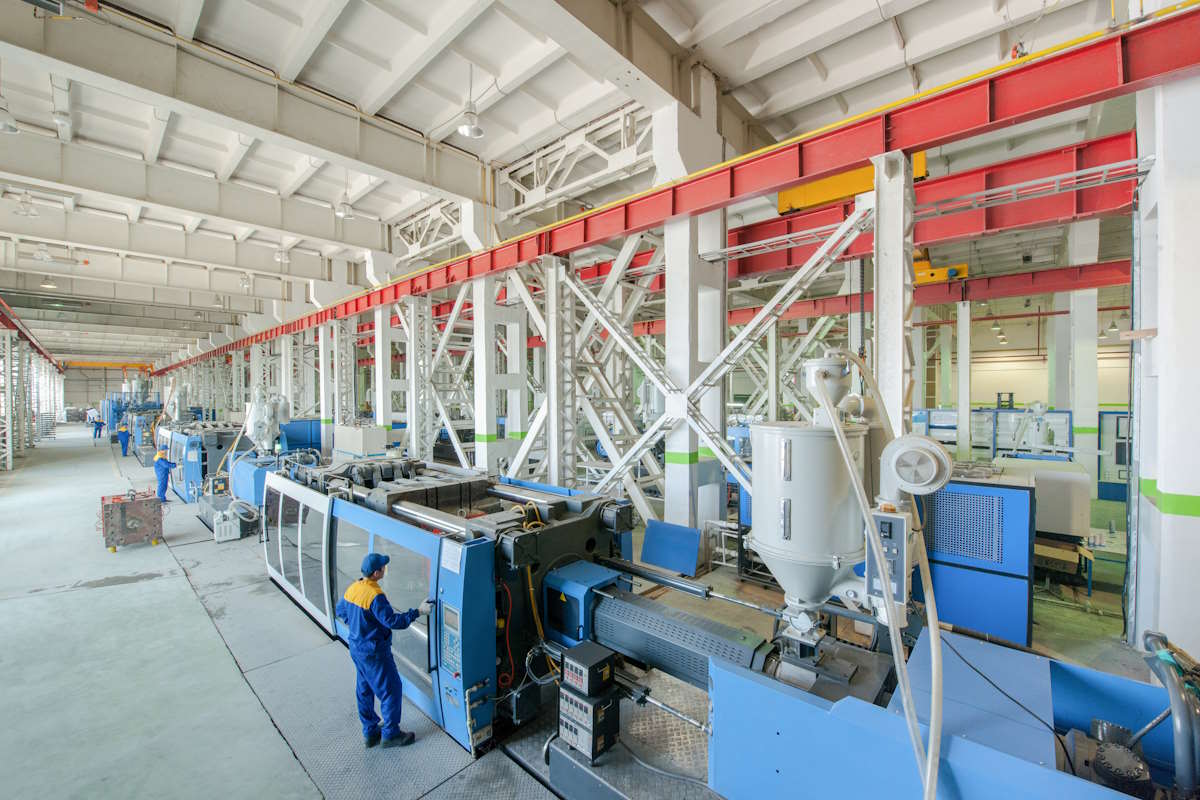
The Importance of Precision in Small-Part Molding
Custom small-part molding is a highly specialized process that focuses on creating intricate components tailored to specific requirements. Whether the need is for high-volume production or prototypes, this approach ensures products meet precise standards. A critical aspect of achieving such precision lies in the design and quality of the injection molding mold parts, which form the foundation of the entire process. These molds are crafted with exceptional accuracy to ensure that every component meets the desired specifications.
High-quality molds enable manufacturers to produce consistent, reliable parts even at high volumes, making them indispensable in industries like medical devices, automotive, and electronics.
Custom molding also offers unparalleled versatility in materials, allowing manufacturers to choose options tailored to specific demands such as heat resistance, strength, or flexibility. This adaptability ensures that small parts can function seamlessly in even the most demanding applications.
Benefits for the Healthcare Industry
The healthcare industry relies heavily on small-part molding for a wide range of applications, including medical devices, surgical tools, and laboratory equipment. Components used in these applications require strict compliance with regulatory standards and exceptional precision to ensure patient safety and efficacy.
Custom small-part molding enables the production of disposable medical parts, such as syringes, catheters, and diagnostic equipment, that meet stringent hygiene requirements. These components often involve biocompatible materials, which are critical for patient-facing applications. The ability to create parts with tight tolerances ensures seamless functionality in devices like insulin pumps and inhalers.
For the healthcare sector, scalability is another significant advantage of custom molding. The process can easily accommodate high production volumes while maintaining consistent quality, making it ideal for mass production of essential medical components.
Transforming Electronics with Precision Parts
Miniaturization and precision are non-negotiable. From smartphones to wearable devices, custom small-part molding solutions are at the forefront of technological innovation.
Injection molding allows manufacturers to create intricate parts for circuit boards, connectors, and casings with exceptional dimensional accuracy. As electronic devices become smaller and more complex, custom molding ensures that components fit perfectly within compact spaces without compromising performance.
Material selection plays a critical role in electronic applications. Conductive and heat-resistant materials are often required to ensure the durability and reliability of parts subjected to electrical currents and high temperatures. Custom molding also supports the integration of overmolding techniques, where two or more materials are combined to create multi-functional components. This capability is particularly useful for producing ergonomic grips or adding protective layers to electronic housings.
Advancing the Automotive Industry
The automotive industry is a prime example of how custom small-part molding contributes to innovation and efficiency. From engine components to interior features, molded parts play a critical role in enhancing vehicle performance and comfort.
Automotive components often face harsh operating conditions, such as extreme temperatures, vibrations, and chemical exposure. Custom molding solutions provide access to materials that can withstand these challenges while maintaining structural integrity. Parts such as connectors, seals, and housings for electronic sensors are manufactured using injection molding to ensure precision and durability.
The automotive sector benefits from the cost-efficiency of custom small-part molding. The ability to produce large quantities of identical parts at a low per-unit cost makes it an attractive option for manufacturers looking to streamline production while maintaining high quality.
Consumer Goods
In the realm of consumer goods, aesthetics, and functionality are equally important. Custom small-part molding enables manufacturers to produce components that meet these dual demands.
Household appliances, personal care products, and packaging solutions often require unique designs to stand out in a competitive market. Injection molding provides the flexibility needed to create visually appealing components while ensuring they are practical and durable. For instance, parts for kitchen gadgets, beauty products, or packaging closures can be tailored to specific sizes, colors, and textures, meeting both brand and consumer expectations.
Custom molding allows for eco-friendly material options, aligning with the growing demand for sustainable consumer products. By selecting biodegradable or recyclable materials, manufacturers can reduce environmental impact without compromising quality.
Meeting Aerospace Standards with Precision
The aerospace industry demands unparalleled precision and reliability, making custom small-part molding an indispensable solution. From lightweight components for aircraft interiors to high-performance parts for engines, molded parts are integral to the sector’s success.
Given the critical nature of aerospace applications, materials used in custom molding must meet strict certifications for strength, heat resistance, and corrosion resistance. The ability to produce lightweight yet robust components is essential for enhancing fuel efficiency and performance.
Custom small-part molding also supports rapid prototyping, enabling aerospace manufacturers to test and refine designs before full-scale production. This capability accelerates innovation while ensuring all parts meet the rigorous standards required for aviation safety.
The Future of Custom Small-Part Molding
As industries continue to evolve, custom small-part molding is poised to become even more integral to manufacturing. Advancements in technology, such as 3D printing and automated systems, are enhancing the precision and efficiency of the molding process.
The growing emphasis on sustainability is also driving innovations in material science. Manufacturers are exploring bio-based polymers and recyclable materials to meet environmental goals while maintaining high performance. Custom molding solutions are uniquely positioned to adapt to these trends, offering flexible and forward-thinking options for a wide range of industries.
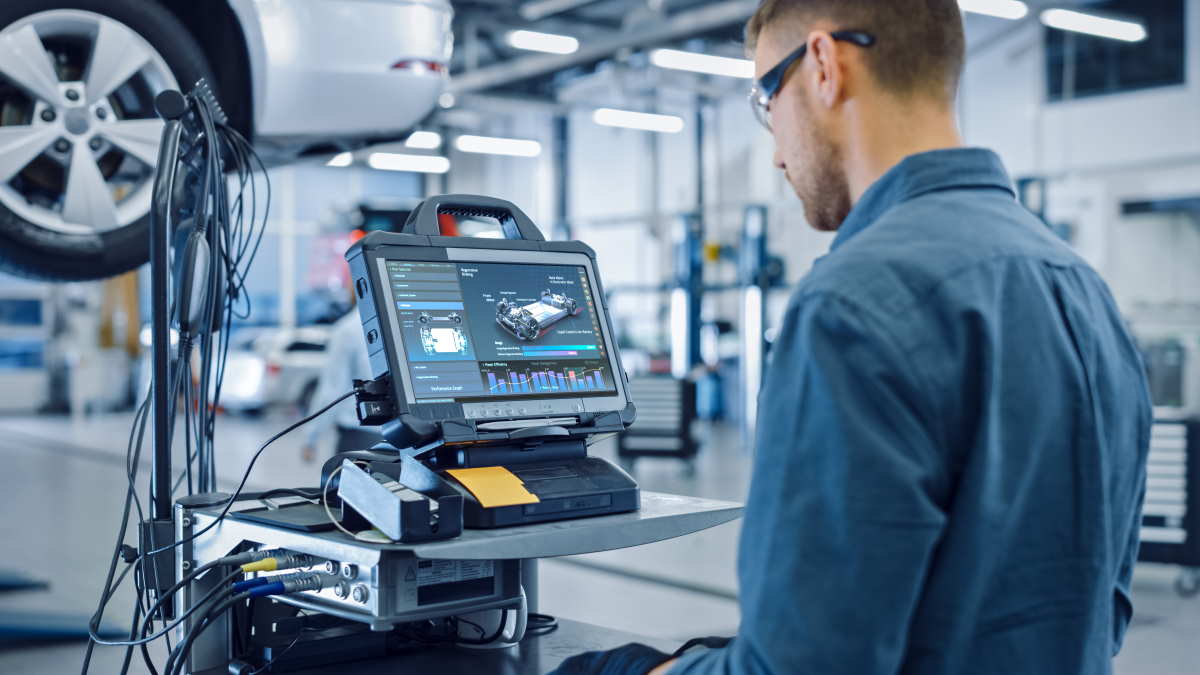
By embracing custom small-part molding, businesses can meet the demands of modern manufacturing with confidence, ensuring they stay ahead in an increasingly competitive landscape. Whether it’s producing life-saving medical devices, cutting-edge electronics, or sustainable consumer goods, the possibilities are limitless.