In modern manufacturing, efficiency and adaptability are key to survival and success. Automation offers incredible potential to enhance productivity, reduce costs, and improve overall quality. However, not every manufacturing process is equally suitable for automation, and jumping in without proper planning can lead to costly mistakes.
Before investing in any new automation technology, manufacturers must take a measured approach, starting with a thorough Automation Assessment. This assessment is crucial in determining which processes are the best candidates for automation and understanding the potential return on investment.
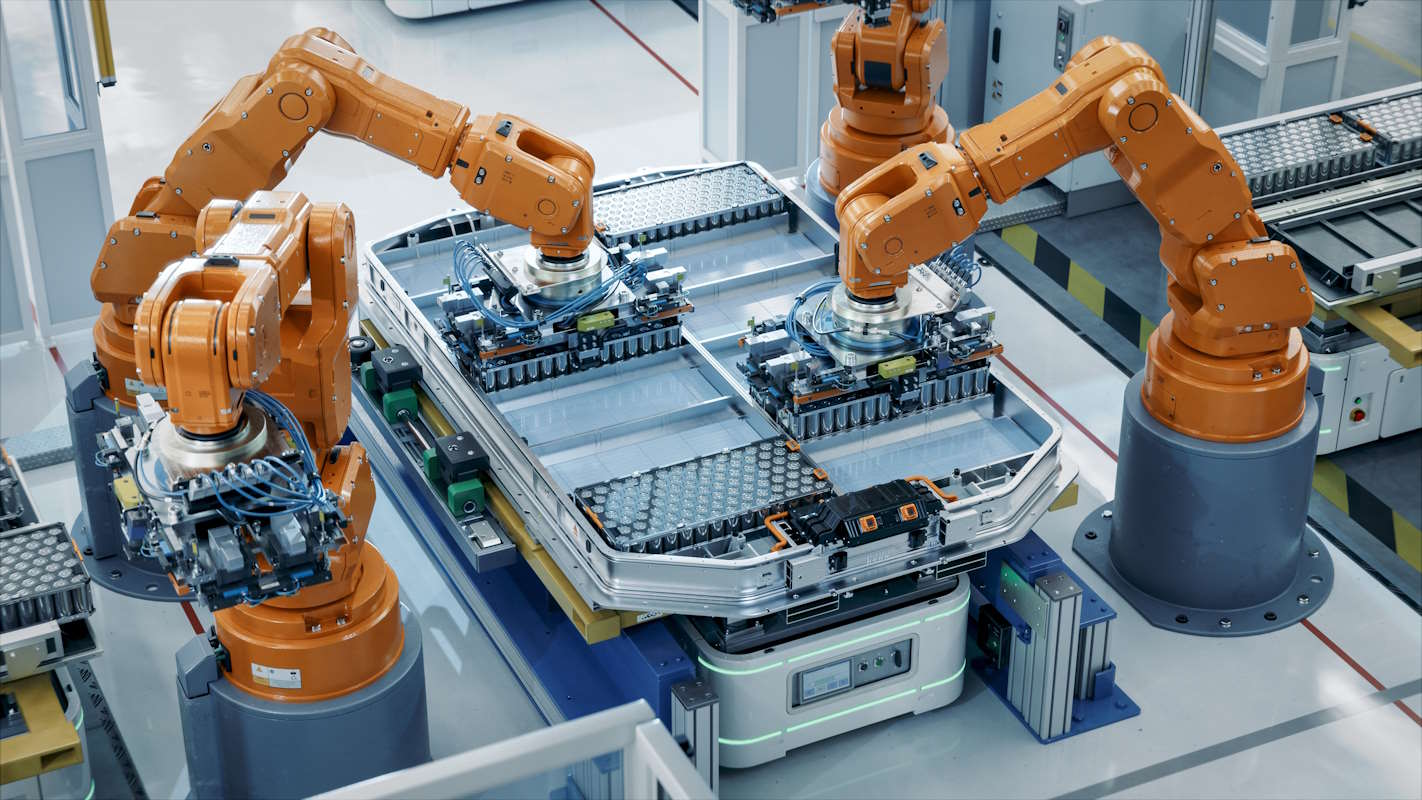
This guide provides a step-by-step approach to help manufacturers decide whether automation is the right option for their specific needs.
Understanding Your Current Operations
The first step of any effective Automation Assessment is a detailed evaluation of your current processes. This includes mapping out the entire manufacturing workflow, from raw material acquisition to product delivery. Manufacturers need to identify bottlenecks, inefficiencies, areas of high labor cost or potential for error.
This involves capturing data on production rates, downtime, defect rates, and any other relevant metrics. This thorough evaluation allows you to understand the weaknesses of your current system and where targeted improvements might have the most impact. It also helps you later determine what areas need to be addressed through automation and which might not be suitable.
Identifying Key Areas for Automation
Once you’ve fully understood your existing processes, it’s time to identify specific areas where automation can be most beneficial.
- Consider repetitive tasks that are time-consuming, error-prone, or physically demanding.
- Look at processes that require a high degree of accuracy and consistency.
- Examine any areas where there is a bottleneck or where delays are common.
This step requires a close analysis of the data gathered in the previous evaluation phase. This approach helps you narrow your focus to targeted areas for improvement and allows you to plan for a staggered implementation instead of an immediate overhaul. A key part of this phase of your Automation Assessment is to rank potential applications for automation by factors such as impact and cost.
Analyzing Feasibility and ROI
Not every process can or should be automated. Before committing to an automation project, manufacturers must conduct a feasibility analysis and calculate the potential return on investment (ROI). This involves considering factors such as equipment cost, software, installation, and ongoing maintenance.
It also means evaluating the potential for increased production, reduced waste, and improved product quality. It’s vital to create a realistic financial plan that incorporates not just the initial costs but also the hidden ROI and potential for growth and expansion using automation.
The feasibility and ROI analysis is the core part of a full Automation Assessment, as it can help inform your decision and guide you on what areas to prioritize.
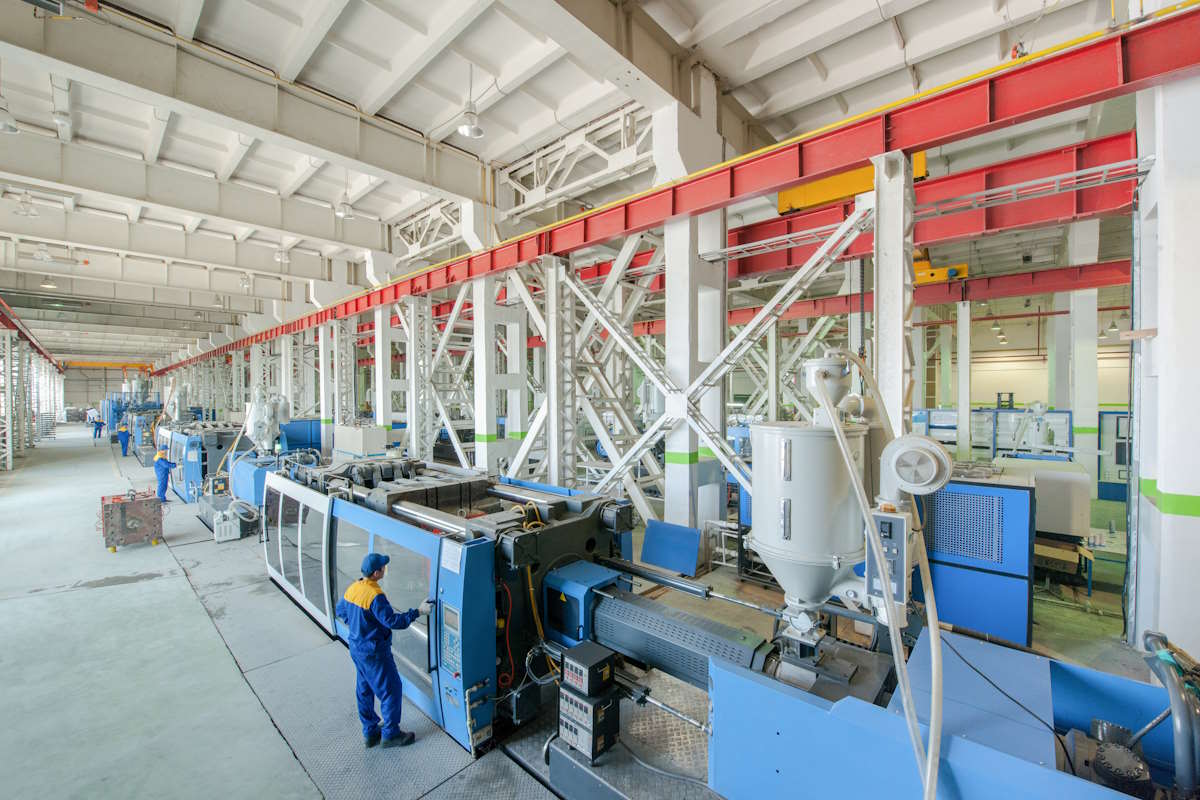
Choosing the Right Automation Technologies
With a clear understanding of the areas for automation and a realistic understanding of the budget and returns, manufacturers must select the right technologies. This means exploring the various automation solutions, from robotics and machine vision systems to advanced process control software and artificial intelligence.
You will have to carefully evaluate potential solutions based on their performance, reliability, cost, and integration with existing systems. It’s important to choose technologies that are not only efficient but also scalable, allowing for future growth. This phase of the Automation Assessment should focus on solutions that meet your particular needs and business goals.
Implementing and Monitoring
Once the automation technologies have been chosen, the implementation phase needs to be planned carefully. This may involve a pilot program to test the new systems before full deployment. That allows you to make adjustments before a full-scale rollout.
Of course, it’s crucial to establish a plan to monitor performance and fine-tune the new automated processes. That means measuring key metrics such as throughput, uptime, and defect rates. Continuous monitoring allows you to spot any issues and optimize the performance of your newly automated systems.
Are You Ready for the Future of Manufacturing?
A thorough Automation Assessment isn’t just a preliminary step. Rather, it’s the essential foundation upon which any successful automation journey is built. It guides manufacturers through the complexities of technology implementation, ensuring that investments align with strategic objectives.
By embracing a systematic approach that carefully evaluates current processes, identifies key areas for improvement, and analyzes potential return on investment, manufacturers can move forward with confidence. This careful planning not only helps avoid common pitfalls but also ensures that automation initiatives are optimized for long-term success.
Ultimately, a detailed Automation Assessment allows manufacturers to access the full potential of automation, transforming operations and securing a competitive advantage in today’s marketplace.