The heavy equipment industry is a backbone of sectors like construction, mining, and agriculture, where machinery uptime directly impacts productivity and revenue. Traditionally, maintaining and servicing heavy equipment involved manual tracking, paper-based workflows, and reactive maintenance approaches. However, with advancements in heavy equipment software, field service management (FSM) has evolved into a data-driven, predictive, and highly efficient system.
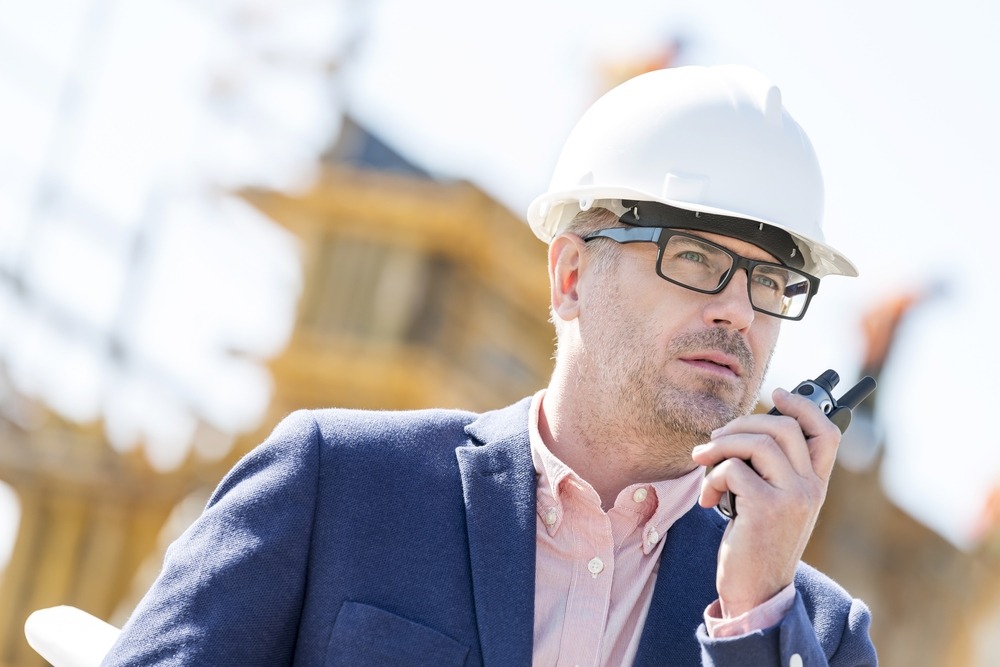
The Need for Digital Transformation in Heavy Equipment Management
Field service organizations are rapidly shifting from paper-based workflows to mobile applications to enhance efficiency. The demand for digital solutions is driven by:
- Increasing equipment complexity – Modern machinery incorporates IoT sensors, requiring sophisticated diagnostic tools.
- Rising operational costs – Equipment downtime costs can range from $500 to $1,000 per hour in industries like construction and mining.
- Strict compliance requirements – Heavy equipment must adhere to environmental and safety regulations, which are challenging to manage manually.
Key Features of Modern Heavy Equipment Software
Heavy equipment software enhances field service operations through several key features:
1. Predictive Maintenance and IoT Integration
Predictive maintenance, enabled by IoT, helps companies reduce unplanned downtime. Predictive maintenance can reduce maintenance costs and eliminate breakdowns. IoT-enabled FSM solutions collect real-time data from machines, identifying issues before they cause failures.
2. AI-Powered Scheduling and Dispatching
AI-driven scheduling optimizes technician assignments based on location, skill set, and availability. Using AI for field service dispatching increases in workforce productivity and reduces travel time.
3. Digital Work Orders and Mobile Applications
Field service organizations are adopting mobile applications for real-time job updates, work order management, and customer communication. This shift enhances efficiency and ensures seamless information flow between field technicians and back-office teams.
4. Inventory and Parts Management
Equipment downtime often results from delayed part replacements. FSM software with real-time inventory tracking helps businesses maintain optimal stock levels. Companies using automated inventory management substantially reduce spare part shortages.
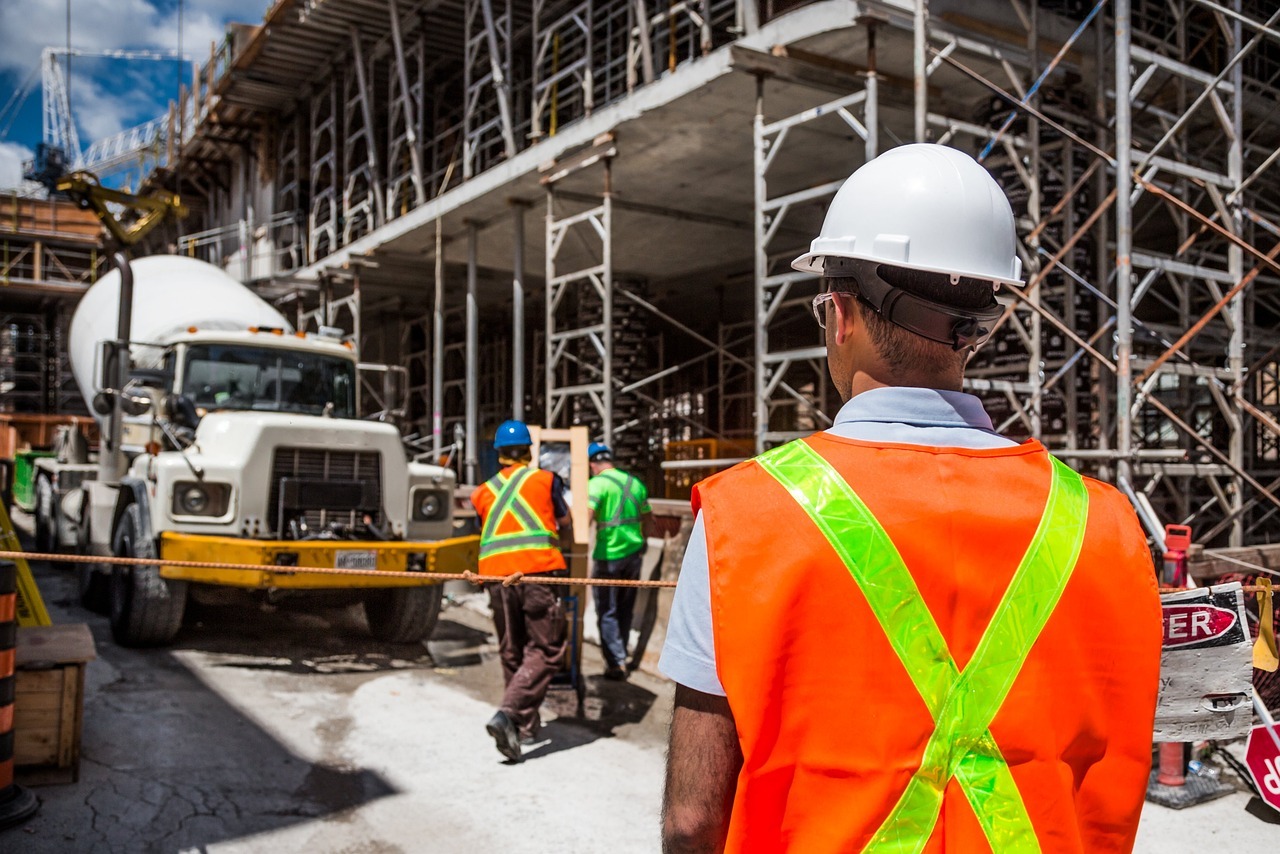
Business Impact of Implementing FSM in Heavy Equipment
Companies that adopt heavy equipment software experience significant improvements:
- Increased Equipment Uptime: Predictive maintenance reduces downtime by up to 45%.
- Enhanced First-Time Fix Rates: Optimized scheduling and mobile access to equipment manuals increase first-time fix rates by 30%.
- Cost Reduction: Automated workflows and AI-driven dispatching cut operational costs by 25-30%.
- Regulatory Compliance: Digital tracking of maintenance logs simplifies compliance with safety and environmental regulations.
Future Trends in FSM for Heavy Equipment
The future of field service management in heavy equipment is being shaped by emerging technologies:
- Augmented Reality (AR) for Remote Assistance – AR-based remote guidance can reduce technician travel costs by 30%.
- Blockchain for Service Records – Secure, immutable service logs improve transparency in maintenance history.
- Machine Learning for Automated Diagnostics – AI-driven diagnostics are expected to enhance issue detection and troubleshooting by 40% in the next five years.
Conclusion
The adoption of heavy equipment software is no longer optional for businesses looking to remain competitive in the heavy machinery sector. With predictive maintenance, AI-powered scheduling, and digital workflows, FSM solutions are reshaping the industry, ensuring efficiency, cost savings, and compliance. As technology advances, organizations that embrace these innovations will gain a significant edge in field service operations.
For companies seeking to optimize their heavy equipment management, leveraging FSM software is the key to maximizing productivity and minimizing downtime. Explore how the latest solutions can transform your operations today.