The modern freight forwarding industry operates in a 24/7 global environment where shipments cross time zones, customer inquiries arrive at all hours, and critical decisions must be made regardless of physical location. Traditional office-based customer relationship management systems simply cannot support the dynamic, distributed nature of international logistics operations. As freight forwarding companies expand their global reach, mobile workforce management and sophisticated CRM solutions have become essential infrastructure for maintaining competitive customer service and operational efficiency.
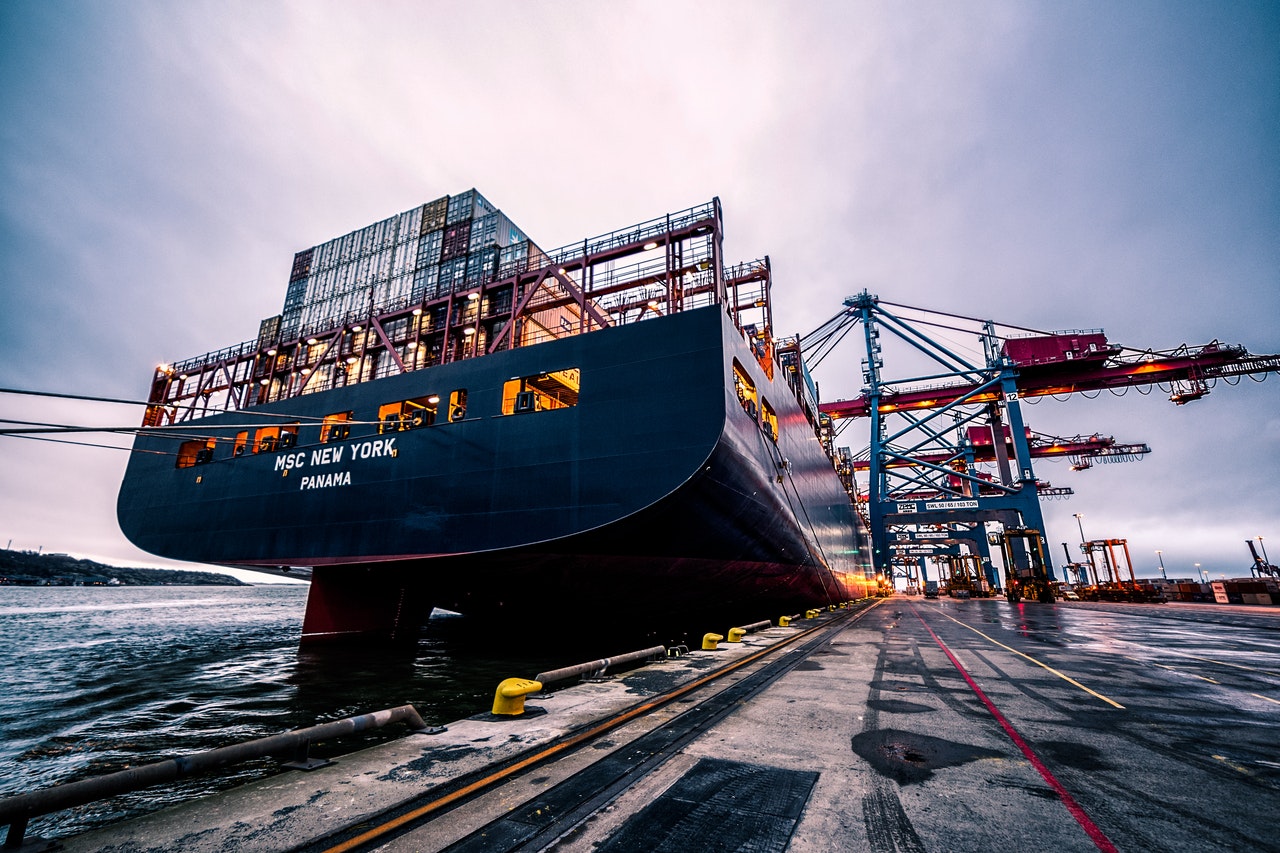
The Global Challenge: Managing Customer Data Across Time Zones
International freight forwarding presents unique challenges in customer data management that extend far beyond simple contact information storage. When a shipment moves from Shanghai to Los Angeles, it involves multiple stakeholders across different time zones, regulatory environments, and operational systems. A single customer inquiry about shipment status might require coordination between origin agents, destination handlers, customs brokers, and delivery teams operating in completely different time zones.
The complexity multiplies when considering that freight forwarding customers often require immediate responses to time-sensitive questions. A manufacturer in Germany discovering a production delay needs to communicate changes to their freight forwarder instantly, regardless of whether it’s 2 AM in the forwarder’s home office. Traditional CRM systems designed for standard business hours cannot accommodate these global operational realities.
Modern mobile CRM solutions address these challenges through cloud-based architectures that enable real-time data synchronization across all global locations. When a customer service representative in Hong Kong updates a shipment record, that information becomes immediately available to colleagues in London, New York, and Sydney. This synchronization ensures consistent customer communication regardless of which team member handles the inquiry.
The most sophisticated systems also incorporate intelligent routing that automatically directs customer inquiries to the most appropriate team member based on time zone availability, language preferences, and specialized expertise. This ensures that customers receive knowledgeable responses even when their primary contact is unavailable due to time zone differences.
Mobile Access: Bringing the Office to the Field
The mobile revolution in freight forwarding extends far beyond simple email access. Modern logistics operations require field personnel to access complete customer histories, shipping documentation, and real-time tracking information while visiting ports, warehouses, and customer facilities. Traditional paper-based systems or laptop-dependent processes create significant limitations for field operations.
Advanced mobile CRM platforms provide comprehensive access to customer information, including historical shipment data, preferred routing options, special handling requirements, and communication preferences. When a field representative visits a customer’s facility, they can access the complete relationship history, enabling more informed discussions about service improvements and expansion opportunities.
Document management through mobile platforms has become particularly crucial for international freight operations. Customs brokers need immediate access to commercial invoices, bills of lading, and certificates of origin while working at port facilities. Mobile CRM systems that integrate with document management platforms enable secure access to these critical documents from any location with internet connectivity.
The integration of mobile photography and document scanning capabilities allows field personnel to capture and immediately share important information with global teams. When port inspections reveal packaging issues or customs authorities request additional documentation, field representatives can instantly document the situation and share it with relevant stakeholders worldwide.
HIPAA Compliance: Managing Sensitive Cargo Information
The transportation of pharmaceutical products and medical devices introduces complex regulatory compliance requirements that significantly impact CRM system design and implementation. HIPAA regulations and international equivalent standards require stringent data protection measures that extend beyond traditional freight forwarding security protocols.
Pharmaceutical shipments often require detailed temperature monitoring, chain of custody documentation, and restricted access to shipment information. Mobile CRM systems handling these sensitive cargo types must incorporate advanced encryption, role-based access controls, and comprehensive audit trails that track every interaction with shipment data.
The challenge intensifies when considering that pharmaceutical shipments often involve multiple parties with different access requirements. Manufacturing facilities need comprehensive shipment visibility, while distribution centers may only require delivery scheduling information. Mobile CRM platforms must provide granular permission controls that ensure each stakeholder accesses only the information necessary for their specific role.
Compliance documentation represents another critical aspect of pharmaceutical freight forwarding. Mobile systems must maintain detailed records of temperature excursions, handling procedures, and custody transfers that meet regulatory requirements across multiple jurisdictions. This documentation must be immediately accessible to regulatory authorities while maintaining appropriate security controls.
Synchronization: Bridging Office and Field Operations
The effectiveness of mobile workforce management depends entirely on seamless synchronization between office-based systems and field operations. Traditional approaches that rely on manual data entry or batch processing create significant delays and error opportunities that can impact customer service quality.
Real-time synchronization enables office personnel to track field activities and provide immediate support when needed. When a field representative encounters customs clearance issues, office-based specialists can immediately access the same shipment information and provide remote assistance. This coordinated approach reduces resolution time and improves customer satisfaction.
The synchronization extends to financial systems, enabling field personnel to access customer credit information, approve additional charges, and process payments while on-site. This capability is particularly valuable for international shipments where unexpected charges or service modifications are common.
Advanced synchronization also enables predictive analytics that can anticipate customer needs and operational challenges. By analyzing historical data patterns, mobile CRM systems can alert field representatives to potential issues before they occur, enabling proactive customer communication and problem resolution.
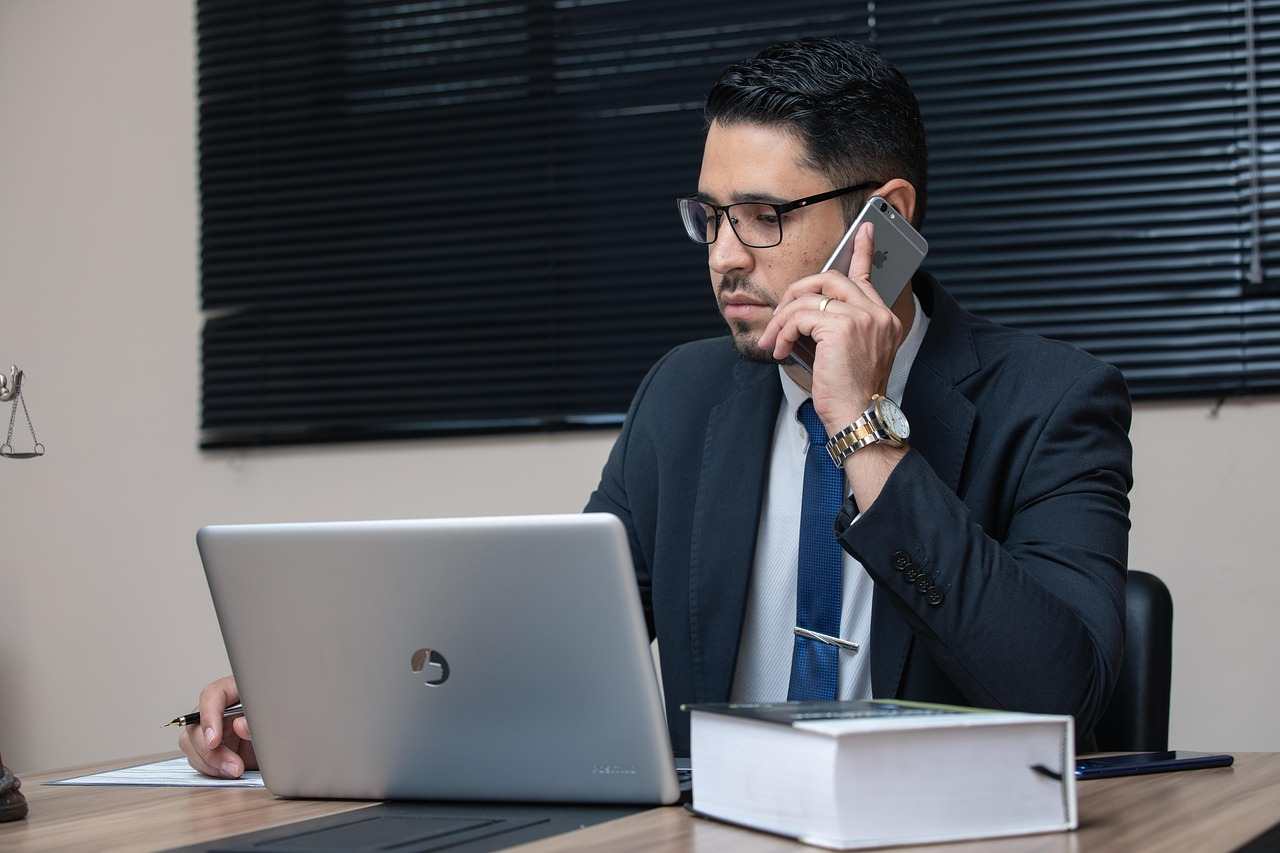
Customer Communication Management During International Shipments
International shipments involve complex communication requirements that span multiple time zones, languages, and cultural contexts. Effective customer communication management requires sophisticated systems that can coordinate messaging across global teams while maintaining consistent brand voice and service standards.
Mobile CRM platforms enable coordinated communication strategies that ensure customers receive timely updates regardless of shipment complexity. Automated notification systems can send proactive updates about customs clearance, delivery scheduling, and potential delays while allowing field personnel to provide personalized follow-up when needed.
The integration of translation services and cultural adaptation features helps ensure effective communication across diverse international markets. When a Chinese freight forwarder handles shipments to multiple countries, mobile CRM systems can automatically adapt communication styles and content to meet local cultural expectations and language preferences.
Multi-channel communication management ensures that customers can reach freight forwarders through their preferred communication methods, whether email, phone, messaging apps, or web portals. Mobile CRM systems that integrate these channels provide field personnel with complete conversation histories, enabling more informed and personalized customer interactions.
Technology Integration and Implementation Strategies
Successful mobile workforce management requires careful integration with existing freight forwarding systems, including transportation management systems, customs clearance platforms, and financial management tools. The most effective implementations create seamless workflows that eliminate duplicate data entry and reduce operational complexity.
API integration enables mobile CRM systems to automatically import shipment data, update tracking information, and synchronize customer communications across all platforms. This integration eliminates manual data entry while ensuring that all stakeholders have access to current information.
Cloud-based architectures provide the scalability and reliability needed for global freight forwarding operations. These platforms can handle varying usage patterns across different time zones while maintaining consistent performance standards regardless of user location.
Security considerations become particularly important when implementing mobile workforce management systems. Advanced encryption, secure authentication protocols, and comprehensive access controls ensure that sensitive customer and shipment information remains protected while enabling the flexibility needed for global operations.
Performance Metrics and Continuous Improvement
Mobile workforce management systems provide unprecedented visibility into field operations and customer service performance. Advanced analytics can track response times, resolution rates, and customer satisfaction scores across different locations and service types.
The data collected through mobile CRM systems enables continuous improvement in operational efficiency and customer service quality. By analyzing patterns in customer inquiries, service requests, and operational challenges, freight forwarders can identify opportunities for process improvements and service enhancements.
Predictive analytics applied to mobile workforce data can anticipate staffing needs, identify potential service disruptions, and optimize resource allocation across global operations. This intelligence enables proactive management decisions that improve operational efficiency and customer satisfaction.