Asset management can be a significant challenge for businesses today, especially as they expand and accumulate more resources. Properly tracking assets ensures that companies understand their inventory, streamline operations, and reduce costs. The advent of technology has allowed organizations to embrace more efficient and effective strategies for asset tracking, making it easier than ever to keep tabs on essential resources. Below are six tech-based tips to follow when tracking your assets for optimal management.
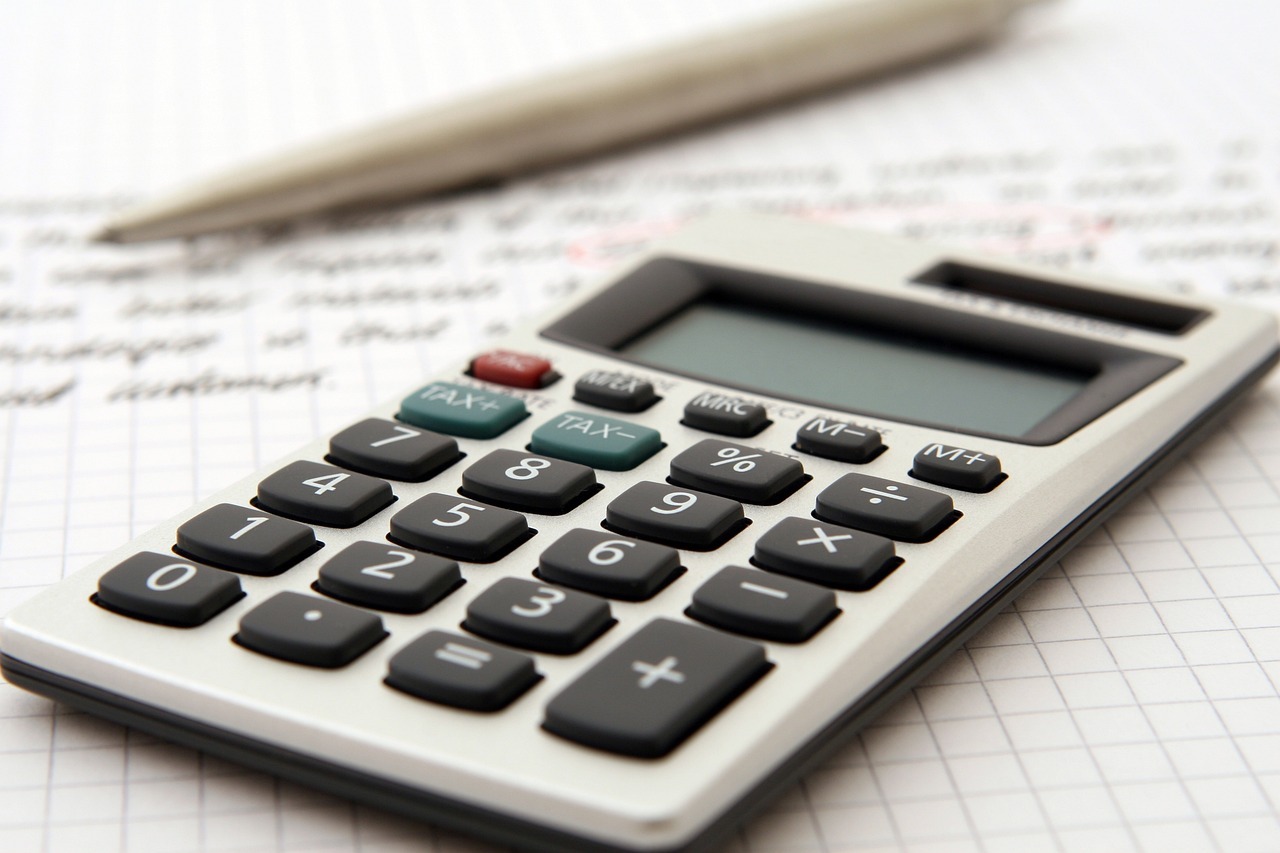
Implement a Bluetooth Solution
The rise of Bluetooth technology has transformed the way businesses approach asset tracking. This wireless technology allows devices to communicate over short distances, making it ideal for connecting an array of asset tags to a central system. Using a Bluetooth solution for asset tracking offers several advantages, including real-time monitoring and increased accuracy in locating items. Additionally, this method supports a range of devices, which helps organizations maintain an effective inventory without extensive manual checks. Integrating ble tracking in your processes can provide a systematic approach to managing assets while saving time and resources. By leveraging Bluetooth asset tracking, businesses can achieve seamless integration with other tech tools such as smartphones and tablets, empowering employees to quickly locate items. Whether you are tracking equipment, valuable inventory, or sensitive materials, this technology can streamline the process, ensuring you never lose sight of critical resources.
Utilize GPS Tracking for Mobile Assets
For businesses managing mobile assets—such as vehicles, heavy machinery, or portable equipment—GPS tracking provides significant advantages. This technology offers reliable real-time location data, enabling organizations to monitor the movements of their assets efficiently. A well-implemented GPS tracking system can help companies reduce loss, improve logistics, and enhance customer service. Investing in GPS tracking solutions enhances security, as businesses can quickly pinpoint the location of their valuable items. Additionally, GPS systems can often integrate with fleet management software, allowing for consolidated visibility and reporting. The ability to analyze location patterns can also contribute to optimized routes and fuel efficiency.
Embrace RFID Technologies
Radio Frequency Identification (RFID) is another powerful tool for tracking assets effectively. RFID systems work by using tags that transmit information via radio waves, providing automatic tracking without the need for manual scanning. This technology can significantly streamline inventory management, allowing companies to keep very accurate counts of their resources without expending much labor. With RFID, businesses can identify assets from a distance, reducing the time it takes to conduct inventory checks. This method is especially beneficial in environments with a high volume of assets, as it minimizes human error. By employing RFID systems, organizations create a more organized approach to asset tracking, enhancing operational efficiency. Visit Metalcraft’s site to learn more.
Implement Asset Management Software
Making use of specialized asset management software is key for any organization’s tracking needs. These software solutions can centralize data collection, streamline inventory audits, and enhance reporting capabilities. Many modern systems offer cloud-based functionalities, allowing for access from anywhere and ensuring that all users can view real-time asset status. Moreover, the integration of automation features facilitates regular updates and notifications. Businesses benefit from more nuanced data analysis, such as usage and maintenance records, which contribute to proactive decision-making. When selected and implemented effectively, asset management software can enhance both tracking accuracy and overall productivity.
Consider IoT Solutions
The Internet of Things (IoT) is rapidly changing how assets are monitored and managed. By incorporating IoT devices into your asset-tracking strategy, businesses can create a robust tracking ecosystem that provides real-time data. Smart sensors, tags, and devices communicate through a centralized hub, allowing companies to maximize efficiency and maintain complete visibility over their assets. IoT solutions enable businesses to gather data about asset usage, condition, and location, providing critical insights to enhance decision-making. Predictive maintenance can also be facilitated through IoT, ensuring that issues are addressed before they become serious problems. By leveraging IoT technology, organizations can transform their asset management approaches to be more intelligent and responsive.

Foster a Culture of Accountability
While technology plays an essential role in effective asset tracking, fostering a culture of accountability is equally important. Employees must understand the significance of asset management and take responsibility for the tools they utilize. Training staff on the importance of accurate asset tracking helps instill a sense of ownership. Regular workshops and reminders about best practices can encourage employees to remain engaged and proactive in their asset management duties. By promoting a culture of accountability, organizations can ensure that technological advancements are fully utilized and that all members contribute to efficient inventory and asset management. Assuring proper tracking of assets is no longer an uphill battle in our tech-driven world.
By implementing these six tech-based approaches, businesses can enhance operational efficiency, reduce losses, and ensure that resources are effectively managed. The integration of advanced solutions allows organizations to keep pace with their evolving asset management needs, making it easier to achieve a seamless and productive operation.